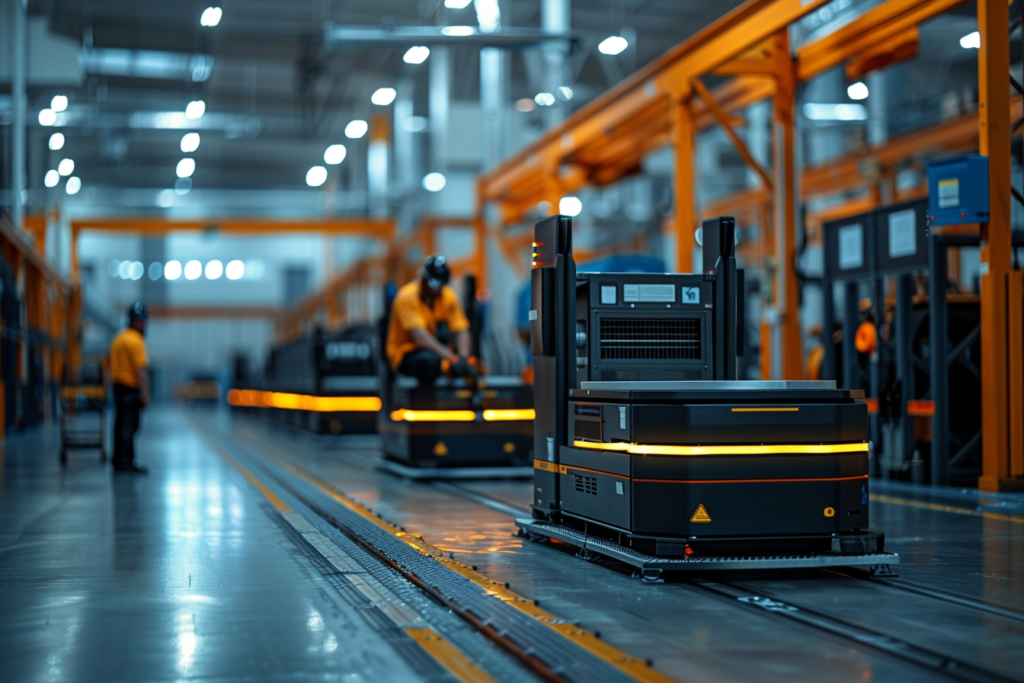
L’installation d’un Miniload est une étape cruciale pour optimiser les opérations de stockage automatisé dans un entrepôt. Cependant, des erreurs courantes peuvent compromettre l’efficacité et la sécurité du système. Cet article explore les erreurs à éviter lors de l’installation d’un Miniload pour garantir une mise en service réussie et durable. Ensemble, découvrons les erreurs à éviter et les bonnes pratiques concernant l’installation et la gestion de vos Miniloads.
Mauvaise évaluation des besoins
Une évaluation incorrecte des besoins peut entraîner l’installation d’un système inadapté.
Analyse insuffisante de la capacité de stockage
Ne pas prendre en compte les besoins réels en termes de volume et de poids des marchandises à stocker. Une estimation précise des besoins en stockage est cruciale pour déterminer la taille et la capacité du Miniload à installer. Il est important de considérer les pics de demande saisonniers, les rotations de stock et la variété des produits pour éviter les surcharges ou les sous-utilisations du système.
En sous-estimant les volumes, l’entreprise risque de se retrouver rapidement à court d’espace, nécessitant des investissements supplémentaires. À l’inverse, une surestimation peut conduire à un gaspillage de ressources et d’espace. Une analyse détaillée et précise permet d’optimiser les coûts et l’efficacité de l’installation.
Ignorance des exigences spécifiques de l’entrepôt
Négliger les particularités de l’entrepôt, telles que la hauteur sous plafond, la surface disponible et les flux de travail. Chaque entrepôt a ses propres contraintes architecturales et opérationnelles. Une analyse approfondie de l’espace disponible et des chemins de circulation des marchandises doit être réalisée pour garantir une installation fluide et efficace du Miniload, tout en optimisant l’utilisation de l’espace vertical et horizontal.
L’intégration harmonieuse du Miniload dans l’infrastructure existante est essentielle pour éviter les interruptions et les inefficacités dans les opérations quotidiennes. Prendre en compte les particularités de l’entrepôt dès le départ permet de maximiser l’efficacité et de minimiser les ajustements coûteux post-installation.
Choix inapproprié de l’emplacement
L’emplacement du Miniload influence grandement son efficacité et sa sécurité.
Proximité des autres équipements
Installer le Miniload trop près d’autres machines peut entraîner des interférences et des risques d’accidents. Il est essentiel de prévoir un espace suffisant entre les équipements pour permettre un accès facile pour l’entretien et les réparations, ainsi qu’une circulation fluide des marchandises. De plus, des interférences électromagnétiques ou des vibrations provenant d’autres machines peuvent affecter les performances du Miniload.
Assurez-vous que le Miniload est placé dans une zone où il peut fonctionner de manière optimale sans être entravé par d’autres équipements. Un mauvais positionnement peut également compliquer les flux de travail, créant des inefficacités et des risques de collisions entre les machines.
Accessibilité pour la maintenance
Ne pas prévoir un accès suffisant pour les interventions de maintenance peut compliquer les réparations et les inspections régulières. Un bon accès permet aux techniciens de maintenance d’effectuer des inspections régulières, des réparations rapides et des remplacements de pièces sans perturber les opérations. Un accès difficile peut prolonger les temps d’arrêt et augmenter les coûts de maintenance.
L’accessibilité doit inclure des passages sécurisés et suffisamment d’espace autour du Miniload pour que les techniciens puissent travailler confortablement et en toute sécurité. Prendre en compte ces besoins lors de la phase de planification permet de réduire les interruptions et d’assurer une maintenance efficace et rapide.
Installation non conforme aux normes
Le respect des normes de sécurité et des recommandations du fabricant est essentiel.
Non-respect des normes de sécurité
Ignorer les directives de sécurité peut entraîner des risques pour les opérateurs et les équipements. Les normes de sécurité incluent des protocoles pour l’installation, l’utilisation et la maintenance des systèmes automatisés. Il est important de suivre ces normes pour minimiser les risques d’accidents, de blessures et de dommages aux biens.
Les normes de sécurité couvrent plusieurs aspects, tels que la stabilisation correcte du Miniload, l’installation de dispositifs de protection, et la garantie que toutes les connexions électriques et mécaniques sont conformes aux spécifications du fabricant. Une installation négligente peut conduire à des accidents graves et à des arrêts prolongés des opérations.
Utilisation de composants non homologués
Utiliser des pièces ou des composants non certifiés peut compromettre la fiabilité du Miniload. Les composants homologués sont conçus et testés pour fonctionner en harmonie avec le système global. L’utilisation de pièces non certifiées peut entraîner des incompatibilités, des pannes fréquentes et une diminution de la durée de vie du Miniload.
L’utilisation de pièces non homologuées peut également annuler les garanties du fabricant, ce qui peut entraîner des coûts élevés en cas de réparations ou de remplacement de pièces. Il est donc crucial de s’assurer que tous les composants utilisés sont certifiés et recommandés par le fabricant du Miniload.
Mauvaise intégration avec les systèmes existants
Une intégration défaillante peut limiter les performances du Miniload.
Incompatibilité logicielle
Ne pas vérifier la compatibilité avec les systèmes de gestion de l’entrepôt (WMS) existants peut entraîner de sérieux problèmes opérationnels. Une intégration logicielle réussie permet une communication fluide entre le Miniload et les autres systèmes de gestion, améliorant ainsi la coordination et l’efficacité des opérations. Une incompatibilité peut entraîner des erreurs de données, des interruptions de service et une inefficacité générale.
Pour garantir une bonne intégration, il est essentiel de :
- Évaluer les systèmes actuels : Examiner les logiciels et les technologies déjà en place pour s’assurer qu’ils peuvent communiquer efficacement avec le nouveau Miniload.
- Consulter les fournisseurs : Travailler avec les fournisseurs de WMS et de Miniload pour valider la compatibilité et réaliser des tests avant l’installation complète.
- Planifier la transition : Développer un plan de transition qui minimise les interruptions de service et assure une intégration en douceur.
Coordination insuffisante avec les autres systèmes automatisés
Négliger la synchronisation avec les convoyeurs, les robots et autres équipements automatisés peut entraîner des goulots d’étranglement et des inefficacités dans le flux de travail. Une coordination efficace garantit que tous les systèmes travaillent ensemble de manière harmonieuse, optimisant le flux des marchandises et réduisant les temps de traitement.
Pour assurer une bonne synchronisation :
- Étudier les flux de travail : Analyser les flux de marchandises et identifier les points où les systèmes doivent interagir.
- Utiliser des interfaces standardisées : Mettre en place des interfaces de communication standardisées entre les différents systèmes pour faciliter l’intégration.
- Effectuer des tests de performance : Réaliser des tests de performance pour s’assurer que les systèmes peuvent fonctionner ensemble sans problème.
Formation insuffisante du personnel
Le personnel doit être correctement formé pour utiliser et entretenir le Miniload.
Manque de formation initiale
Ne pas fournir une formation complète aux opérateurs sur le fonctionnement du Miniload peut entraîner des erreurs de manipulation et des inefficacités. Une formation initiale adéquate assure que les opérateurs comprennent les fonctionnalités du système, les procédures de sécurité et les méthodes de résolution des problèmes courants. Cela réduit les erreurs de manipulation et améliore l’efficacité opérationnelle.
Une formation initiale efficace devrait inclure :
- Présentation des équipements : Explications détaillées sur le fonctionnement et les composants du Miniload.
- Procédures de sécurité : Instruction sur les pratiques de sécurité et les protocoles d’urgence.
- Simulation de scénarios : Exercices pratiques pour familiariser les opérateurs avec les situations courantes et d’urgence.
Absence de programmes de formation continue
Ne pas mettre en place des sessions de mise à jour régulières pour le personnel peut entraîner une obsolescence des compétences. La formation continue permet aux opérateurs de se tenir au courant des nouvelles fonctionnalités, des mises à jour logicielles et des meilleures pratiques en matière de maintenance et de sécurité. Cela garantit que le personnel est toujours capable de tirer le meilleur parti du Miniload.
Les programmes de formation continue devraient inclure :
- Sessions de recyclage : Révisions régulières des compétences de base et des procédures de sécurité.
- Mises à jour technologiques : Formation sur les nouvelles fonctionnalités et les mises à jour du système.
- Ateliers de résolution de problèmes : Ateliers interactifs pour résoudre les problèmes courants et améliorer les pratiques opérationnelles.
Maintenance préventive négligée
Une maintenance régulière est essentielle pour assurer la longévité et l’efficacité du Miniload.
Absence de plan de maintenance
Ne pas établir un calendrier de maintenance préventive peut entraîner des pannes imprévues et des arrêts prolongés. Un plan de maintenance détaillé et régulier permet d’identifier et de résoudre les problèmes potentiels avant qu’ils ne causent des défaillances majeures. Cela inclut des inspections périodiques, des ajustements, et le remplacement de pièces usées.
Pour mettre en place un plan de maintenance efficace, il est essentiel de :
- Établir un calendrier : Planifier des intervalles réguliers pour les inspections et les entretiens.
- Documenter les procédures : Créer des guides détaillés pour chaque tâche de maintenance.
- Suivre les performances : Utiliser des outils de suivi pour surveiller l’état et la performance du Miniload.
Inspections irrégulières
Omettre les inspections régulières pour détecter les problèmes potentiels peut réduire la durée de vie du Miniload et augmenter les coûts de réparation. Les inspections régulières permettent de surveiller l’état des composants, de détecter les signes d’usure et de prévenir les pannes imprévues.
Pour garantir des inspections régulières :
- Check-lists de contrôle : Utiliser des check-lists pour s’assurer que tous les aspects critiques sont inspectés.
- Personnel formé : Assurer que les techniciens sont formés pour identifier les signes d’usure et les problèmes potentiels.
- Rapports d’inspection : Tenir des rapports détaillés de chaque inspection pour suivre les tendances et planifier les interventions nécessaires.
L’installation d’un Miniload nécessite une planification minutieuse et une exécution rigoureuse. En évitant ces erreurs courantes, les entreprises peuvent garantir une installation réussie et durable, optimisant ainsi leur système de stockage automatisé. En évaluant correctement les besoins, en choisissant le bon emplacement, en respectant les normes, en intégrant harmonieusement les systèmes, en formant le personnel et en assurant une maintenance régulière, les entreprises peuvent maximiser les avantages de leur Miniload et minimiser les risques.
Article généré par la technologie Open AI