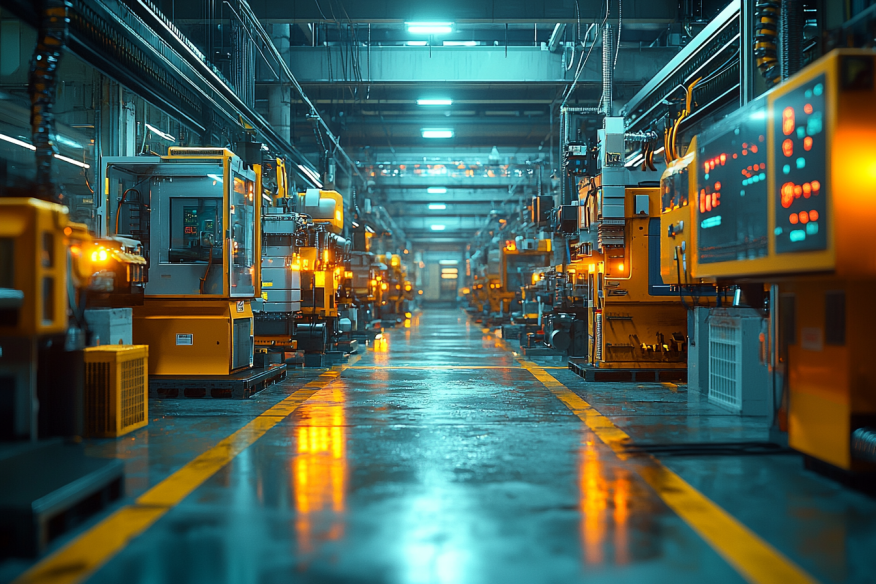
Les systèmes automatisés jouent un rôle clé dans les entrepôts modernes, offrant des performances accrues et une meilleure gestion des flux logistiques. Cependant, leur fiabilité repose sur une maintenance rigoureuse et bien exécutée. Des erreurs de maintenance, qu’elles soient organisationnelles ou techniques, peuvent entraîner des pannes coûteuses, des arrêts prolongés et une diminution de la durée de vie des équipements. Cet article identifie les erreurs les plus courantes en maintenance des systèmes automatisés et explore des solutions pratiques pour les éviter. En adoptant une gestion proactive et en formant correctement les équipes, les entreprises peuvent optimiser leurs opérations, réduire les temps d’arrêt et prolonger la durée de vie de leurs équipements automatisés.
Les erreurs liées à la planification de la maintenance
Une maintenance bien planifiée est essentielle pour garantir la continuité des opérations et la performance des systèmes automatisés. Pourtant, une mauvaise organisation de cette maintenance peut entraîner des pannes évitables, une augmentation des coûts et des interruptions fréquentes des flux logistiques.
Absence de maintenance préventive
De nombreuses entreprises se concentrent uniquement sur la maintenance corrective, intervenant uniquement lorsque les équipements tombent en panne. Cette approche, bien que courante, engendre des coûts élevés et des interruptions imprévues. Par exemple, un simple capteur négligé peut provoquer une défaillance majeure du système, paralysant l’entrepôt pendant des heures, voire des jours.
Solution : Mettre en place une maintenance préventive rigoureuse. Cela inclut des contrôles réguliers et une vérification systématique des composants clés avant qu’ils ne s’usent ou ne tombent en panne.
Fréquences d’interventions mal définies
Un autre problème courant réside dans la définition inappropriée des fréquences d’intervention. Des intervalles trop longs augmentent le risque de pannes majeures, tandis que des intervalles trop courts entraînent des coûts inutiles et une usure prématurée des pièces.
Exemple : Programmer une inspection hebdomadaire pour un système qui nécessite uniquement un entretien mensuel peut engendrer des interruptions inutiles et des dépenses superflues.
Solution : Adopter une approche basée sur les recommandations des fabricants et les données des équipements pour ajuster la fréquence des maintenances en fonction de leur utilisation réelle et des signes d’usure.
Les erreurs techniques lors des interventions de maintenance
Même avec une planification bien établie, des erreurs techniques peuvent survenir pendant les interventions. Ces erreurs, souvent dues à des imprécisions ou à un manque de préparation, peuvent nuire aux performances des systèmes automatisés et compromettre leur fiabilité.
Utilisation d’outils inappropriés
Les systèmes automatisés nécessitent des outils spécifiques pour garantir des interventions précises et éviter d’endommager les équipements. Pourtant, il n’est pas rare que des techniciens utilisent des outils standards inadaptés, ce qui peut provoquer des dommages irréversibles.
Exemple : L’utilisation d’une clé non calibrée sur un composant sensible peut entraîner un désalignement ou une casse, aggravant le problème initial.
Solution : Fournir aux techniciens un kit d’outillage spécialement conçu pour les équipements automatisés. De plus, une vérification régulière de l’état des outils doit être effectuée pour éviter tout dysfonctionnement lié à leur usure.
Négligence dans le respect des protocoles
Les systèmes automatisés fonctionnent selon des spécifications précises, et chaque étape d’entretien doit être respectée scrupuleusement. Une simple négligence, comme l’omission de calibrer un capteur ou de vérifier une connexion électrique, peut entraîner des pannes importantes.
Exemple : Un capteur mal ajusté pourrait envoyer des données erronées, perturbant l’ensemble du processus logistique.
Solution : Établir des checklists détaillées pour chaque intervention et s’assurer que les techniciens suivent rigoureusement les protocoles établis par les fabricants.
Les erreurs de gestion des données de maintenance
Dans le cadre de la maintenance des systèmes automatisés, la gestion des données est souvent sous-estimée. Une mauvaise utilisation ou un suivi insuffisant des informations peut conduire à des interventions inefficaces et des pannes récurrentes.
Manque de traçabilité
L’absence d’un historique clair des opérations de maintenance est une erreur fréquente. Sans documentation précise des interventions passées, il devient difficile d’identifier les problèmes récurrents ou d’analyser les causes sous-jacentes des défaillances.
Exemple : Si un équipement tombe en panne plusieurs fois pour une raison similaire, mais que les données des précédentes réparations ne sont pas disponibles, le technicien risque de répéter les mêmes actions sans résoudre le problème de manière définitive.
Solution : Mettre en place un logiciel de gestion de maintenance assistée par ordinateur (GMAO). Ce type d’outil permet de centraliser toutes les informations relatives aux équipements : historique des interventions, état des composants, et recommandations des fabricants.
Mauvaise analyse des données collectées
Les systèmes automatisés modernes sont souvent équipés de capteurs qui génèrent une grande quantité de données, comme les vibrations, la température ou les performances des moteurs. Toutefois, ces données restent inutiles si elles ne sont pas correctement interprétées et exploitées.
Exemple : Ignorer une augmentation progressive des vibrations détectée par un capteur peut entraîner une panne majeure, alors qu’une intervention préventive aurait pu éviter l’arrêt de la machine.
Solution : Former les équipes à analyser les données fournies par les capteurs et les outils de diagnostic. Ces informations doivent être utilisées pour anticiper les pannes, ajuster les cycles de maintenance et optimiser les performances des équipements.
Les solutions pour éviter ces erreurs courantes
Pour garantir la fiabilité des systèmes automatisés et réduire les risques liés aux erreurs de maintenance, il est crucial d’adopter des stratégies et des outils adaptés. Ces solutions permettent d’optimiser les interventions, de prolonger la durée de vie des équipements et de réduire les coûts liés aux arrêts imprévus.
Formation continue des techniciens
L’évolution constante des technologies impose une mise à jour régulière des compétences des équipes. Des techniciens bien formés sont en mesure de manipuler les équipements automatisés correctement, d’identifier rapidement les anomalies et de suivre rigoureusement les protocoles de maintenance.
Exemple : Un technicien formé à l’utilisation des capteurs intelligents pourra mieux interpréter les données collectées et anticiper une panne avant qu’elle ne survienne.
Solution : Organiser des sessions de formation régulières pour les équipes, avec un focus sur les nouvelles technologies et les meilleures pratiques en maintenance. Inclure également des simulations pour renforcer leurs compétences face à des scénarios réels.
Automatisation et digitalisation des processus de maintenance
L’automatisation des processus de maintenance est un levier puissant pour réduire les erreurs humaines et améliorer l’efficacité des interventions. Les outils comme les logiciels GMAO permettent de planifier, suivre et optimiser chaque opération.
Exemple : Un logiciel GMAO peut envoyer des alertes automatiques lorsqu’un équipement atteint un seuil critique, comme un niveau élevé de vibrations ou une consommation énergétique inhabituelle.
Solution : Intégrer des capteurs connectés et des logiciels de gestion pour surveiller les performances des équipements en temps réel. Cela permet de détecter les anomalies précocement et de programmer des interventions ciblées avant qu’un problème majeur ne survienne.
Collaboration avec des experts en maintenance
Certaines interventions complexes nécessitent l’expertise de professionnels externes, comme les fabricants ou les fournisseurs des équipements automatisés. Travailler avec ces experts permet d’assurer des diagnostics précis et des réparations efficaces.
Exemple : Faire appel à un fournisseur pour recalibrer un système automatisé complexe peut prévenir des erreurs coûteuses et garantir une optimisation maximale de l’équipement.
Solution : Établir des partenariats avec des experts externes pour les interventions critiques, tout en renforçant la collaboration entre les techniciens internes et ces spécialistes.
La maintenance des systèmes automatisés est une étape essentielle pour garantir leur fiabilité, leur performance et leur longévité. Cependant, des erreurs fréquentes, qu’elles soient liées à la planification, aux interventions techniques ou à la gestion des données, peuvent entraîner des coûts élevés et des interruptions d’activité. En adoptant une approche proactive et structurée, il est possible d’éviter ces erreurs courantes. La formation continue des équipes, l’utilisation d’outils modernes comme les logiciels de gestion de maintenance, et la collaboration avec des experts externes constituent des solutions efficaces pour optimiser les interventions.Investir dans une maintenance bien pensée, c’est non seulement réduire les risques de pannes, mais aussi renforcer la compétitivité et la rentabilité de l’entreprise. Prenez dès aujourd’hui les mesures nécessaires pour garantir la fiabilité de vos systèmes automatisés et maximiser leur potentiel.
Article généré par la technologie Open AI