STACKER | Nanoload
B SYSTEM’S a innové et conçu le Nanoload afin de proposer une toute nouvelle classe d’efficacité, de rentabilité pour ses clients. Conçus par notre bureau d’études, fabriqués dans nos ateliers, cette toute dernière génération de robot de stockage automatisé a été conçue pour générer un retour sur investissement record pouvant démarrer sous les 18 mois.
Le Nanoload®, également connu sous le nom de système de stockage automatisé pour charges légères, ou encore ASRS pour Automated Storage Retrieval System, est une nouvelle technologie utilisée pour le stockage massique très haute cadence. Spécialement adapté au secteur du e-commerce, ce système se compose de rayonnages où les articles sont stockés dans des bacs, des cartons ou des contenants spécifiques. La spécificité du Nanoload® réside dans sa capacité à être à la fois juxtaposé et superposé afin de décupler la cadence du système. Comme le Miniload, le Nanoload® gère les contenants le long des rayonnages pour placer ou récupérer les articles selon les besoins sur les emplacements de droite ou de gauche selon l’axe transversal.
Le Nanoload® optimise l’utilisation de l’espace vertical en permettant un stockage en hauteur, réduisant ainsi l’empreinte au sol nécessaire pour le stockage. Pour chaque allée de stockage, un ascenseur d’entrée et un ascenseur de sortie des articles mis en contenant permet d’éviter tout croisement de flux, et assurant une alimentation et une sortie régulière des articles. Il améliore également l’efficacité des opérations de manutention en automatisant les processus de récupération et de stockage des articles, ce qui réduit le besoin de main-d’œuvre manuelle et minimise les erreurs humaines. Grâce à un logiciel de gestion d’entrepôt, connu sous le nom WMS (Warehouse Management System), le Nanoload® localise en temps réel les demande de destination de flux rentrants et sortants afin de récupérer les articles requis, ce qui accélère la préparation des commandes et améliore le service client.
Les Nanoload® se combinent, tous les 3ml de hauteur libre pour répondre aux besoins et réduire drastiquement le coût global par emplacement.
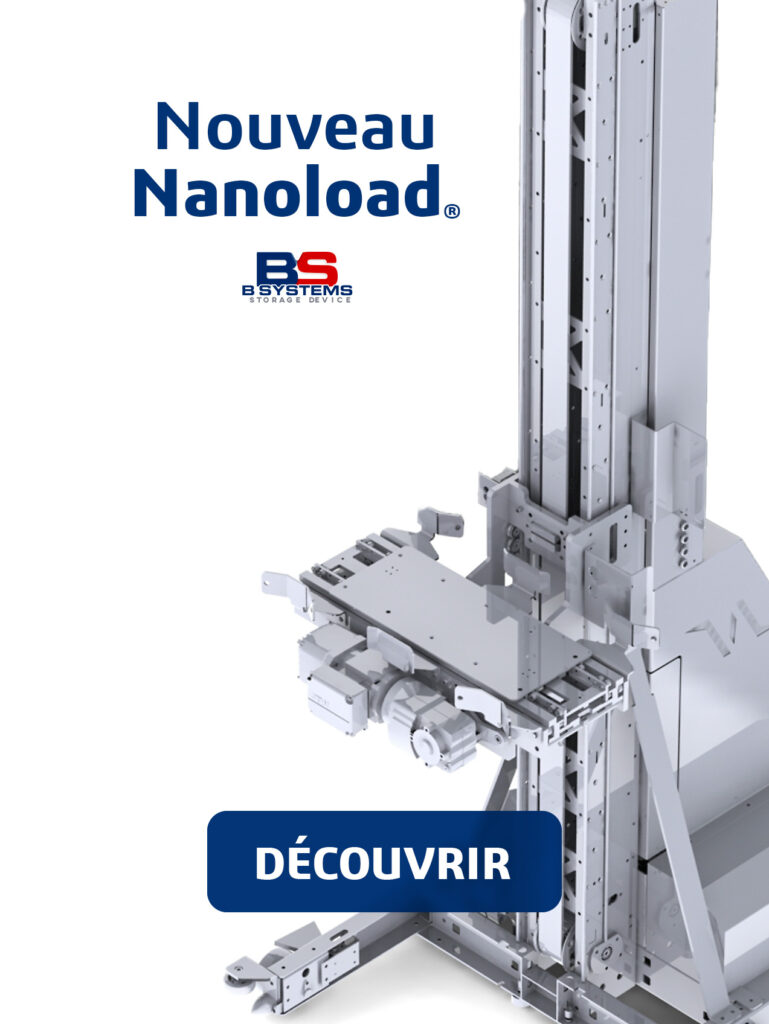

Controls
×- Rotate with the left mouse button.
- Zoom with the scroll button.
- Adjust camera position with the right mouse button.
- Double-click to enter the fullscreen mode.
- On mobile devices swipe to rotate.
- On mobile devices pinch two fingers together or apart to adjust zoom.
- On mobile devices 3 finger horizontal swipe performs panning.
- On mobile devices 3 finger horizontal swipe performs panning.
TOUT CE QU'IL FAUT SAVOIR
Les caractéristiques de nos Nanoloads
Alimentation : 2200w (translation) / 1100w (levage)
Vitesse : 220m/min (translation) / 40m/min (levage)
Hauteur : 3000mm
Accélérations : 3m/s² (translation) / 1m/s²(levage)
Positionnement SSI – BUS profisafe
NANOLOAD standard 50Kg double profondeur avec la fourche télescopique TFDD_L_800
NANOLOAD standard 20Kg simple profondeur avec le mini-gripper MG64 ou MG43
POURQUOI CHOISIR NOS NANOLOADS?
Les avantages du Nanoload B SYSTEM'S
Découvrez les différents avantages de la solution de Nanoload proposée par BSYSTEMS !
Les Nanoloads proposent une capacité de stockage en double profondeur, avec une charge utile jusqu’à 50Kg.
Besoin énergétique très bas par cycle : masse du Nanoload® 480Kg.
Utilisable 24H/24, maintenable allée par allée (ne coupe pas l’installation complète)
Protocole de communication éprouvé pour le positionnement en boucle fermée : SSI
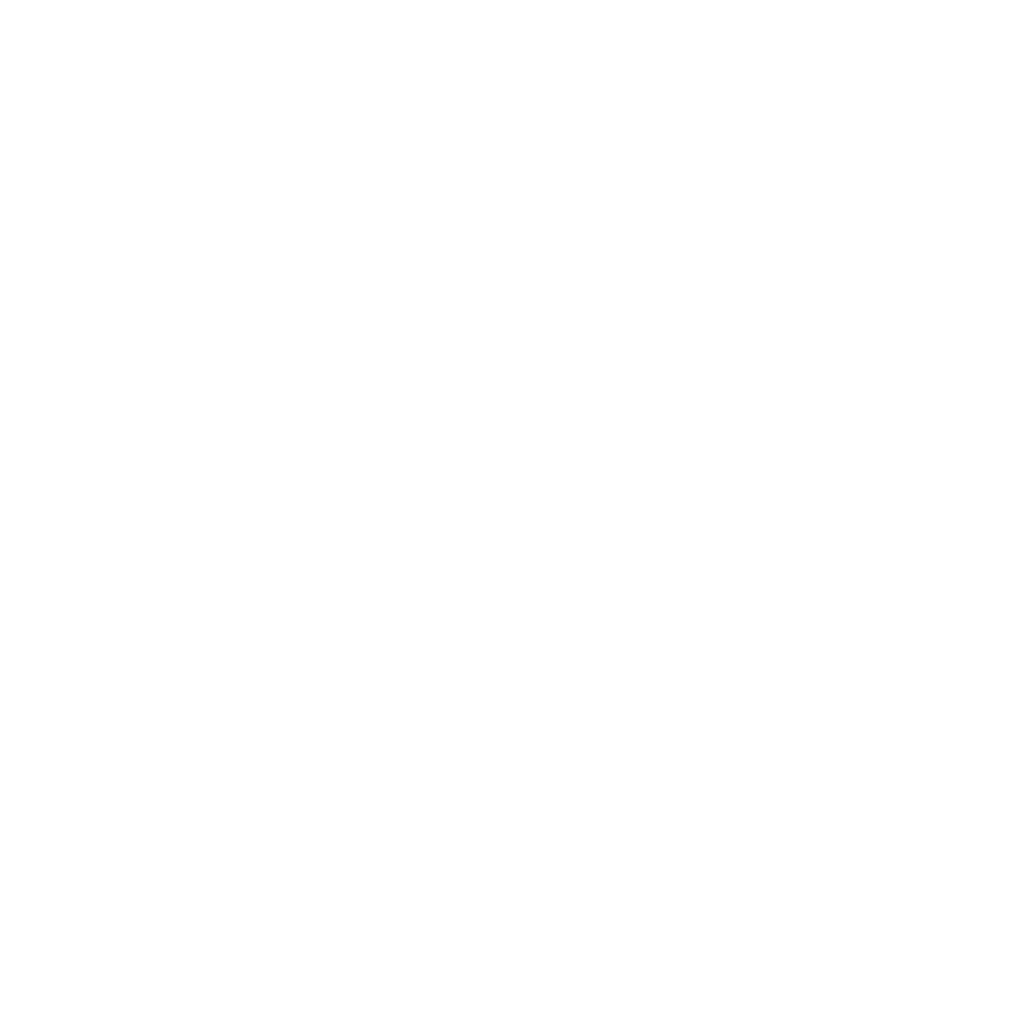
Préhenseur double profondeur
Préhenseur double profondeur (à droite et à gauche, soit 4 profondeurs de stockage à chaque niveaux).
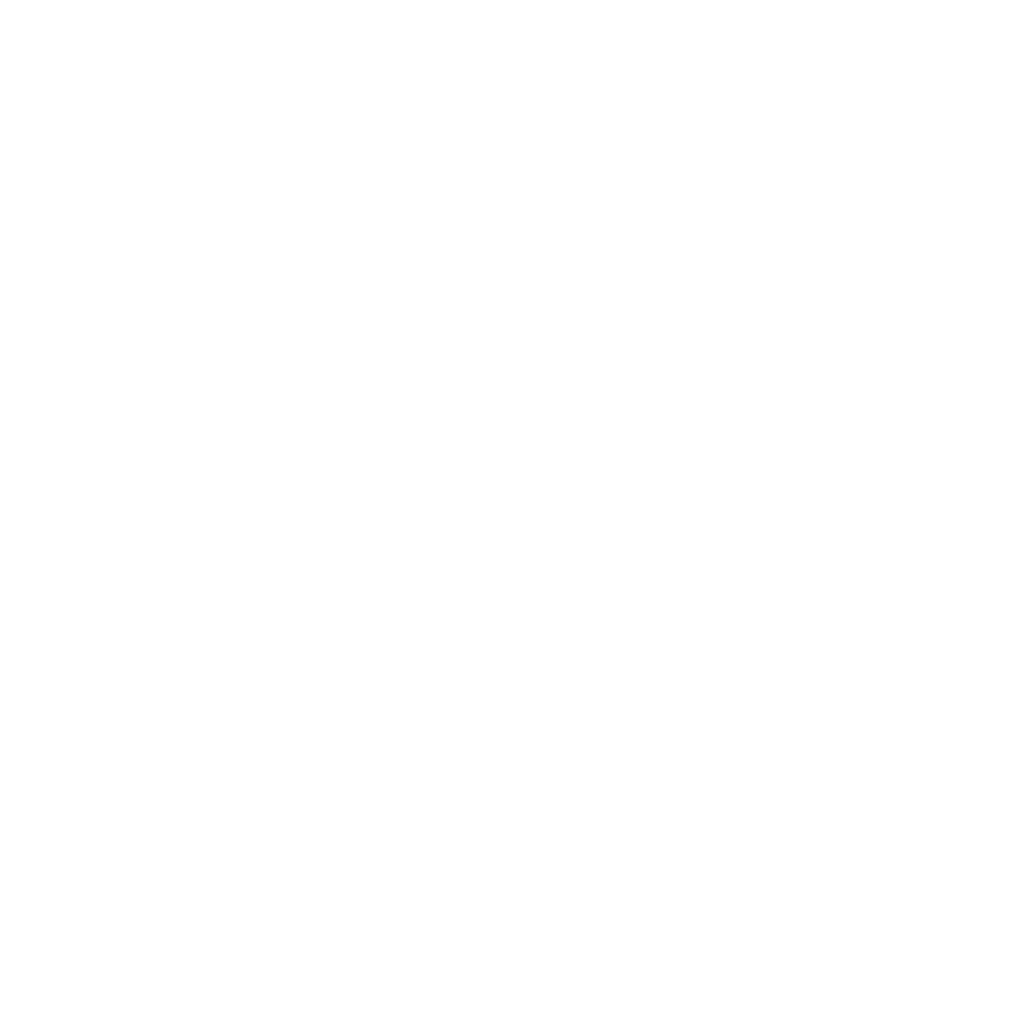
Coûts réduits
Coûts de maintenance le moins cher du marché grâce à la technologie Nanoload.
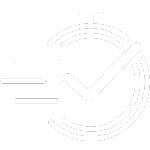
Ultra rapide
Vitesse de déplacement ultra rapide : jusqu’à 220m/min.
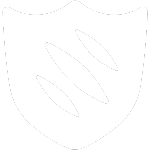
Résistant
Robot conçut sans soudure structurelle, en assemblage complexe ultra rigide afin de résister durablement aux fortes accélérations/freinage.
LES DETAILS
Les caractéristiques du Nanoload
Découvrez les caractéristiques de notre Nanoload, marque déposée par BSYSTEM’S
Application | Type | Ref | CMU |
---|---|---|---|
Double profondeur carton / bac plastique 600x400 ou 400x300 | Nanoload avec TFDD_L_800 | NL_TFDD_L_800 | 50 |
Simple profondeur bac plastique 400x300 | Nanoload avec Minigripper MG43 | NL-MG43 | 20 |
Simple profondeur bac plastique 600x400 | Nanoload avec Minigripper MG64 | NL-MG64 | 20 |
F.A.Q
Tout ce qu'il faut savoir des Nanoloads
Nanoload®, marque déposée par B SYSTEM’S dans plus de 30 pays dans le monde, symbolise la nouvelle génération de robots de stockage.
Les Nanoload®, se singularise par une technologie optimisée des flux à l’aide de composants clés :
- Rayonnages : Des échelles de racks standardisées reçoivent des accessoires adaptatifs aux standards B SYSTEM’S et permettent l’accueil des Nanoload sur rails de roulements latéraux, ces rayonnages sont spécialement étudiés se composent Les rayonnages peuvent s’étendre sur plusieurs niveaux, optimisant ainsi l’utilisation de l’espace vertical.
- Nanoload® : Shuttle multi-niveaux ultra rapide automatisé haute vitesse qui se déplacent sur les axes horizontaux et verticaux le long des rayonnages pour placer ou récupérer les articles en simple ou double profondeur. Nanoload®, sont équipés de nos fourches standard TFDD800_600.
- Systèmes de gestion d’entrepôt (WMS) : Logiciels de traçabilité utilisé et optimisé afin de gérer les flux entrants et sortants pour permettre un zéro défaut et garantit une cadence globale adapté aux fortes demandes.
- Système de manutention au sol : Grâce aux standards B SYSTEM’S, la ligne complète de manutention au sol permet un équipement adapté suivant les besoins : nombre de picking, volume d’accumulation, ligne d’entrée, poste d’association contenant/contenu…
Les Nanoload®, dernière évolution dans le monde du stockage automatisé pour le stockage de petits et moyens articles dans des environnements à haute densité. Ils sont particulièrement adaptés aux opérations nécessitant une préparation rapide des commandes, une haute précision dans la gestion des stocks, et une réduction des coûts de main-d’œuvre. Grâce à un retour sur investissement record, les Nanoload® font prendre une longueur d’avance sur toute concurrence, que ce soit les navettes à empilement de bacs, shuttle ou tout autre système similaire et classique.
Le fonctionnement des Nanoload® repose sur une automatisation embarquée, relié au sol par une communication optique de sécurité. Le process est réalisé de la manière suivante :
- Réception des Articles : Les articles destinés à être stockés dans le Nanoload®, sont identifiés à l’aide du code client (code barre, RFID ou autre), repérés par lecteur et placés dans les contenants (cartons ou bacs plastiques), eux même repérés par un code barre et lus automatiquement par notre dispositif Nanoload®.
Une fois le contenant rempli selon les besoins clients, une simple validation réalise l’opération informatique d’association contenant/contenu et envoie le contenant sur la ligne d’entrée en stock.
- Stockage : Le système informatique de gestion d’entrepôt (WMS) guide le contenant jusqu’au Nanoload grâce à des lecteurs de contenants permettant de réaliser de manière sûre son aiguillage jusqu’au convoyeur d’entrée du Nanoload correspondant à l’emplacement attribué par le WMS. Le Nanoload®, reçoit un ordre de mission de stockage permettant la récupération du contenant en entrée de stock, le transfert au coordonnées émises par le système informatique.
- Récupération des Articles : Dans chaque ordre de fabrication (OF) sont requis pour la préparation des commandes, le WMS envoie des instructions au Nanoload®. Le Nanoload® localise le bac ou le carton contenant les articles nécessaires, le récupère des rayonnages et le transporte jusqu’à la zone de picking ou de préparation des commandes. Ce processus est réalisé de manière rapide et précise, réduisant ainsi le temps nécessaire pour préparer les commandes.
- Préparation des Commandes : L’opérateur suit les instructions situées au poste de picking sur l’IHM tactile prévu à cet effet afin de confectionner le contenant d’expédition simple ou multi-client en fonction des besoins (palette par exemple).
- Retour et Réapprovisionnement : lorsque les articles d’un contenant sont prélevés, l’opérateur valide la fin du picking contenant, les contenants sont soit renvoyés en stock s’ils ne sont pas vides ou si la ligne d’accumulation de contenants vides est pleine, soit renvoyés en ligne d’accumulation afin de procéder à une nouvelle réception articles à stocker. Le cycle de stockage se répète ainsi de manière fluide.
Les Nanoload® est un exécutant des ordres envoyés par l’informatique afin de rendre disponible les articles demandés de la manière la plus fiable, la plus fluide, la plus sûre et rapide.
Optimisation de l’Espace : Chaque Nanoload® permet d’obtenir 4 rangées et de 5 à 11 niveaux suivant la hauteur des contenants, avec une largeur d’allée record de seulement 1000mm.
- Efficacité et Productivité : Grâce à l’informatisation WMS, le dispositif Nanoload® permet une distribution médiane de 3000 contenants par poste de picking et par Nanoload®, soit jusqu’à 12000 contenants par allée, sur une journée de 24H.
- Retour sur investissement record : Le dispositif Nanoload® a été pensé pour réduire au stricte minimum le coût client d’investissement, d’exploitation et de maintenance. Tous frais inclus, il faut en effet compter environ 0.40€HT par cycle entrée/sortie sur 24 mois tout compris, puis environ 0.02€ par cycle entrée/sortie par années suivantes, hors main d’œuvre, selon données Europe 2024.
- Réduction des Coûts de Main-d’œuvre : Grâce au picking mutualisé sur l’ensemble du dispositif, le coût opérateur se situ à environ 0.33€HT par picking entrée ou sortie, selon données Europe 2024.
- Précision et Fiabilité : Chaque maintenance préventive annuelle permet une marche annuelle du dispositif pour l’année suivante.
- Flexibilité Opérationnelle : Les Nanoload® sont à même de gérer le stock de pièces de fabrication, produits semi-finis ou finis.
Contrat type
L’installation d’un système Nanoload® permet de réorganiser vos ressources financières pour votre marketing, votre recherche et développement, la flexibilité et la formation de votre personnel, il est composé de plusieurs éléments :
- Équipement global clé en main :
- Robots Nanoload®,
- Rack d’entreposage,
- Système de manutention au sol,
- Bacs ou cartons de stockage,
- Sécurisation périphérique,
- Contrôle d’accès sécurisé
- Accès maintenance.
- Electrification au sol, faisceau de commande et postes de picking
- Programme WMS pluggé à votre ERP
- Installation et Intégration :
- Le transport,
- L’installation physique de l’équipement dans l’entrepôt.
- Le paramétrage
- les tests préliminaires
- la mise en service de l’équipement.
- Formation du Personnel :
- La formation électromécanique du dispositif
- La formation opérateurs au poste de picking et d’entrée en stock
Coûts d’Exploitation
- Maintenance et Support :
- B SYSTEM’S réalise l’intégralité de la maintenance des systèmes qu’il conçoit et réalise, avec un tarif direct fabricant.
- Énergie :
- Diminution des frais énergétiques par la diminution de l’éclairage sur l’intégralité de la surface de stockage.
- Diminution des frais énergétiques comparativement aux frais que proposent les système shuttle, leur dérivés et chariots élévateurs.
Retour sur Investissement (ROI)
Grâce à nos tarifs direct constructeurs, les Nanoload® B SYSTEM’S offrent des capacités à prix réduits :
- Augmentation de la Productivité :
- Les opérateurs réalisent les pickings à la volée, tout transite de stockage et re stockage s’opère en temps masqué.
- Réduction des Coûts de Main-d’œuvre :
- L’automatisation réduit la main-d’œuvre humaine et permet de décupler vos possibilités de développement en formant votre personnel à des tâches à forte valeur ajoutée.
- Optimisation de l’Espace :
- L’intégralité de la hauteur est exploitée afin de réduire drastiquement l’empreinte au sol.
- Réduction des Erreurs :
- L’automatisation minimise les erreurs humaines, l’ensemble de la chaîne de stockage/déstockage est pris en charge par l’informatique, réduisant ainsi les coûts liés aux erreurs de picking et aux pertes de stock.
- Amélioration du Service Client :
- La rapidité et la précision des Nanoload® permet en seulement quelques minutes de générer l’expédition suite à une commande en ligne par exemple.
- Traçabilité et Gestion des Stocks :
- Les contenants et les articles étant tracés, toute action est maîtrisée depuis l’association contenant / contenu jusqu’au retrait de ou des articles en expédition.
Estimation du ROI
Le ROI d’un système Nanoload® peut varier en fonction de plusieurs facteurs. Plus le stock est haut (nombre d’étages de Nanoload, jusqu’à 4), et long (nombre de travées de stockage, de 1 à 200).
On parle de coût à l’emplacement stocké, en ajoutant les frais du parc de pièces de rechange standard. Il faut également considérer les coûts de maintenance préventive, ou le Nanoload® se démarque une nouvelle fois grâce au multiplexage de niveaux, lorsque les shuttle sont unique par niveau.
En conclusion, l’investissement initial dans un système Nanoload® est en dessous de toutes les autres technologies du marché actuel. Les frais de maintenance sont également divisés par rapport à la concurrence.
Un système Nanoload se compose de robots de stockage au sein d’un rack dédié, d’élévateurs d’entrées et sorties dans le cas ou plusieurs étages sont possibles, et d’une manutention optimisée au sol afin de permettre un traitement optimal des flux de masse.
Nanoloads
Les Nanoloads sont des robots automatisés ultra rapides gérant plusieurs niveaux de stockage contrairement aux systèmes shuttle ou navettes dans les rayonnages pour récupérer et stocker les articles. Ils sont équipés de dispositifs de préhension pour manipuler les bacs ou les cartons. Les Nanoload sont contrôlés par des systèmes de gestion d’entrepôt (WMS) qui optimisent leurs mouvements pour maximiser l’efficacité et minimiser les temps de cycle.
Rayonnages
Les rayonnages sont une base standards industrielle de niveau robotique (exigences plus importante qu’un rack pour chariot élévateur), sur lesquels des accessoires spécifiques B SYSTEM’S sont installés afin d’incorporer les élévateurs, convoyeurs d’entrées/sorties et les Nanoload®.
Bacs et Cartons
Le dispositif Nanoload® sont proposés en standard soit avec des cartons renforcés, soit avec des bacs plastique. Les cartons ayant un pouvoir calorifique moins important que le plastique des bacs.
Systèmes de Gestion d’Entrepôt (WMS)
Le système de gestion d’entrepôt (WMS) est un logiciel de gestion qui permet la traçabilité des articles afin de les ranger, et les sortir à disposition de l’expédition. Il est consultable en temps réel et permet d’observer l’état du stock global.
Convoyeurs
La manutention est standardisée à l’intérieur du rack avec les élévateurs. Dans la zone extérieure de stockage, en zone réception article et expédition, la manutention est réalisée selon l’environnement et les besoins client.
Dispositifs de Prévention et de Sécurité
Le dispositif Nanoload® est une enceinte de stockage fermée et sécurisée permettant de travailler en toute sécurité pour l’ensemble du personnel. Des portillons avec demande d’accès sécurisé permettent d’accéder aux Nanoload® allée par allée.
Systèmes de Contrôle et de Diagnostic
A la moindre alerte, en cas de défaut, un message permet de visualiser et localiser l’anomalie en temps réel et ainsi corriger cette dernière le plus rapidement possible.
Interfaces Utilisateur
Les interfaces utilisateur permettent aux opérateurs d’interagir avec le système Nanoload®. Cela inclut les IHM (écrans tactiles), des radiocommandes pour le service maintenance, des postes de picking et intégration articles.
Un PC équipé de notre logiciel WMS permet la transmission automatique de données avec l’ERP, et l’automatisme embarqué.
Système
- Architecture Système : Les Nanoload® sont intégrés dans une architecture système complète qui comprend des Nanoload®, des rayonnages, des convoyeurs, des bacs, et des logiciels de gestion d’entrepôt (WMS). L’informatique transmet les ordres de l’ERP à l’automatisme, qui à son tour remonte les statuts de missions accomplis et se place en attente de la prochaine.
- Système de Gestion d’Entrepôt (WMS) : Le WMS est le cerveau du système Nanoload®. Il contrôle et optimise les mouvements des Nanoload®, gère les emplacements des articles, et suit les niveaux de stock en temps réel. Le WMS utilise des algorithmes avancés pour maximiser l’efficacité, réduire les temps de cycle et minimiser les erreurs.
- Communication et Réseau : Les systèmes Nanoload® reposent sur des réseaux de communication robustes pour assurer une coordination synchronisée des opérations. Cela inclut la communication entre le WMS, les Nanoload®, les convoyeurs, et les interfaces utilisateur. Les réseaux sans fil ou câblés garantissent des temps de réponse rapides et une fiabilité élevée.
- Interfaces Utilisateur : Les interfaces utilisateur permettent aux opérateurs de surveiller et de contrôler le système Nanoload®. Elles fournissent des informations en temps réel sur les opérations, les niveaux de stock, et les alertes de maintenance. Les interfaces peuvent inclure des écrans tactiles, des terminaux portables, et des applications logicielles sur ordinateurs.
Sécurité
- Sécurité des Opérateurs : La sécurité des opérateurs est une priorité dans les systèmes Nanoload®. Afin de prévenir des risques, tous les accès sont munis de gâches à interverrouillage, avec contrôle d’accès. Toutes les voies d’entrée / sorties sont munies de barrières immatérielles avec fonction mutting pour que seul le passage de contenants soient autorisés.
- Sécurité des Articles : Les Nanoload® sont équipés de systèmes de guidage pour protéger les articles stockés. Le dispositif est équipé également de gabarits optiques permettant le contrôle volumétrique des contenants.
- Sécurité des Données : La partie sécurité et automatisme est contenu dans le système interne, sans connexion externe garantissant la sûreté du programme.
Le WMS est un logiciel à source protégé avec en option un serveur de reprise à chaud.
- Maintenance Préventive : B SYSTEM’S est à même de réaliser 100% de la maintenance de ces équipements, livrés clé en main. Elle permet de garantir un fonctionnement optimal pour l’année à venir.
- Conformité aux Normes : Les systèmes Nanoload® sont conformes aux normes CE. Un bureau de contrôle permet de valider l’installation de votre dispositif Nanoload®.
PROCEDURE
Comment définir un projet de stockage ?
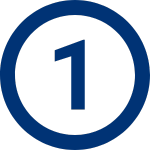
Définir une ou plusieurs tailles de contenants
Avant tout, choisissez une longueur et largeur de contenant (exemple : 600x400). Ensuite , en fonction de vos éléments à stocker, définissez la proportion en hauteur de vos contenants (exemple : 30% ht 320 et 70% ht220)
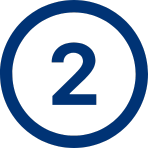
Mesurer votre volume utile disponible
Le volume alloué à votre futur stockage automatisé est prépondérant et influx directement sur : - Les quantités de contenants - Le nombre de Miniloads - La cadence globale du système
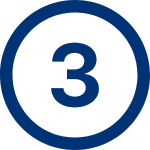
Interface & Manutention au sol
La manutention au sol est conçue de manière standard, mais les ajustements sont nombreux comme : - Position du ou des postes d’entrée produits en stock - Le nombre de poste de picking - Le besoin d’une accumulation tampon de contenants vides
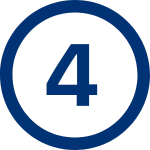
Identifier les besoins présents et futurs
Il est essentiel d’identifier le besoin en cadence d’entrées et sorties maximum par heure, ainsi que le mode de gestion du stock, tel le mode FIFO, à 100% , 50% ou autre.
Besoin d'aide ?
Contactez nous au +33(0) 986 623 547
ou écrivez nous via le formulaire ci-dessous.