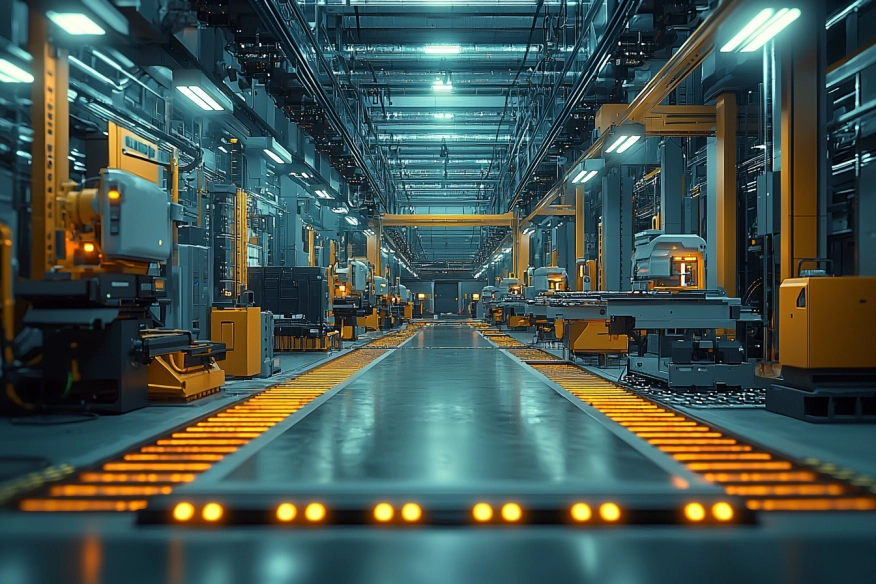
Les systèmes automatisés jouent un rôle essentiel dans les entrepôts modernes, offrant des gains significatifs en termes de productivité et d’efficacité. Toutefois, malgré leur performance, ils ne sont pas exempts de problèmes. Savoir identifier les signes avant-coureurs de dysfonctionnements est crucial pour éviter des interruptions coûteuses et des arrêts prolongés des opérations. Qu’il s’agisse de dégradations mécaniques, de baisses de performance ou d’erreurs logicielles, ces signaux ne doivent pas être ignorés. Cet article vous aide à reconnaître les premiers indicateurs de problèmes dans les systèmes automatisés afin de garantir leur fonctionnement optimal à long terme.
La surveillance des performances des systèmes automatisés
Les systèmes automatisés, tels que les transtockeurs et les miniloads, sont conçus pour fonctionner de manière continue et fluide. Cependant, pour garantir leur efficacité à long terme, il est essentiel de surveiller en permanence leur performance. Une baisse de performance peut être le premier signe d’un problème sous-jacent, qu’il soit mécanique ou logiciel. La surveillance proactive de ces systèmes permet d’intervenir rapidement, avant que les problèmes ne deviennent plus graves.
Les signes d’une baisse de performance
Une des principales alertes indiquant un dysfonctionnement imminent est une réduction progressive de la vitesse des opérations. Par exemple, si un transtockeur prend plus de temps que d’habitude pour se déplacer ou traiter une commande, cela peut signaler une usure des composants ou un problème de calibration. Les temps d’arrêt fréquents, même s’ils sont temporaires, sont également un indicateur clair de dysfonctionnement. Une baisse de la productivité globale de l’entrepôt peut rapidement s’en suivre si ces problèmes ne sont pas identifiés et traités.
Un autre indicateur souvent négligé est la consommation énergétique. Une augmentation soudaine de la consommation d’énergie peut refléter un problème mécanique nécessitant plus de puissance pour accomplir une tâche autrefois simple. Ce type d’anomalie doit être pris au sérieux et analysé pour identifier l’origine du problème avant qu’il ne conduise à une panne totale.
Surveillance des capteurs et des données en temps réel
L’un des avantages majeurs des systèmes automatisés modernes est leur capacité à intégrer des capteurs connectés. Ces capteurs, associés à des technologies comme l’Internet des objets (IoT), permettent de surveiller en temps réel les performances des machines et d’identifier tout écart par rapport aux normes définies. Par exemple, un capteur installé sur un miniload peut envoyer des alertes lorsqu’il détecte des anomalies dans la vitesse de traitement ou dans les vibrations de la machine.
Ces données en temps réel permettent aux gestionnaires d’anticiper les pannes avant qu’elles ne surviennent. En analysant les données collectées par les capteurs, il est possible de repérer des tendances qui indiquent une détérioration progressive des performances. Cela permet non seulement d’intervenir avant qu’un problème majeur n’apparaisse, mais aussi d’optimiser la maintenance prédictive, en effectuant des réparations au moment le plus opportun.
Composants mécaniques : dégradation et dysfonctionnement
Les systèmes automatisés, bien que conçus pour être robustes et fiables, ne sont pas à l’abri de l’usure des composants mécaniques. Ces dégradations peuvent perturber le fonctionnement des machines et, dans le pire des cas, entraîner des pannes complètes. Pour éviter des arrêts d’activité prolongés, il est crucial d’identifier les signes avant-coureurs de défaillances mécaniques.
Bruits inhabituels et vibrations
Un des premiers signes de dégradation mécanique est l’apparition de bruits inhabituels ou de vibrations excessives lors du fonctionnement des machines. Dans des systèmes automatisés comme les transtockeurs ou les miniloads, un bruit anormal peut indiquer qu’une pièce, comme un roulement ou une courroie, commence à s’user. Si ces signes sont ignorés, cela peut rapidement dégénérer en panne totale de la machine. En effet, des vibrations anormales peuvent provoquer un désalignement des pièces, augmentant encore les dommages et l’usure.
Il est donc essentiel d’inspecter régulièrement les machines pour vérifier l’état des composants critiques. Dans certains cas, un simple ajustement ou remplacement de pièces usées suffit à éviter des réparations coûteuses ou des arrêts imprévus de production. Des capteurs de vibration peuvent également être utilisés pour détecter ces anomalies avant même qu’elles ne soient perceptibles par les opérateurs, offrant ainsi une surveillance continue et proactive.
Vérification des pièces mobiles et des courroies
Les pièces mobiles et les courroies sont souvent les premiers éléments à s’user dans un système automatisé. Une courroie mal alignée ou endommagée peut ralentir le processus et entraîner une baisse de productivité. De plus, les roulements, utilisés pour faciliter le mouvement des pièces mobiles, peuvent se détériorer avec le temps, provoquant des frictions supplémentaires et réduisant l’efficacité de la machine.
La maintenance préventive est ici cruciale pour identifier ces problèmes avant qu’ils ne deviennent critiques. Un programme de maintenance bien conçu inclut la vérification régulière des pièces mobiles, le remplacement des courroies usées et l’inspection des roulements. En agissant en amont, les entreprises peuvent éviter des pannes imprévues et prolonger la durée de vie de leurs systèmes automatisés.
Problèmes logiciels et erreurs de programmation
Les systèmes automatisés ne reposent pas uniquement sur des composants mécaniques performants, mais aussi sur des logiciels qui contrôlent l’ensemble de leurs opérations. Lorsque des problèmes surviennent au niveau des logiciels, cela peut provoquer des erreurs imprévues, ralentir les processus ou même causer l’arrêt total du système. Pour garantir la continuité des opérations, il est crucial de repérer les signes avant-coureurs de dysfonctionnements logiciels et de prendre des mesures correctives rapidement.
Signaux d’erreurs logiciels fréquentes
L’un des premiers signes d’un problème logiciel est la fréquence des erreurs ou des alertes système. Si un miniload ou un transtockeur génère régulièrement des alertes pour des opérations échouées ou incomplètes, cela peut indiquer une instabilité du logiciel. Ces erreurs, qu’elles soient liées à des conflits dans les lignes de code ou à des erreurs de communication entre les différents systèmes, perturbent les performances globales.
Une autre alerte concerne les temps de réponse lents du système. Si un système automatisé met plus de temps que d’habitude à exécuter une commande ou à récupérer des informations, cela peut signaler un problème logiciel. Les pannes intermittentes ou la nécessité de redémarrer fréquemment les systèmes pour rétablir leur fonctionnement sont également des indicateurs de dysfonctionnement. Ces symptômes, souvent négligés, peuvent être le signe d’un problème plus profond qui, s’il n’est pas traité rapidement, pourrait entraîner des arrêts de production coûteux.
Importance des mises à jour régulières
Les systèmes automatisés fonctionnent souvent sur des logiciels complexes qui nécessitent des mises à jour régulières pour garantir leur stabilité et leurs performances. Ces mises à jour incluent non seulement des correctifs pour des erreurs existantes, mais aussi des améliorations qui permettent d’optimiser le fonctionnement des machines et de les rendre plus performantes.
Ignorer ces mises à jour peut entraîner des problèmes de compatibilité ou des vulnérabilités dans le système. Par exemple, des incompatibilités entre différentes versions de logiciels peuvent causer des erreurs de communication entre les machines, ralentissant les processus ou provoquant des interruptions. De plus, des failles de sécurité non corrigées peuvent être exploitées par des cyberattaques, mettant en danger l’ensemble de l’infrastructure.
Pour éviter ces risques, il est essentiel de maintenir à jour l’ensemble des logiciels associés aux systèmes automatisés, qu’il s’agisse du logiciel de gestion des commandes ou des programmes qui contrôlent directement les machines. Cela permet d’anticiper les pannes logicielles et d’assurer une stabilité continue des opérations.
L’importance de la maintenance prédictive et préventive
Pour assurer la longévité et l’efficacité des systèmes automatisés, la maintenance prédictive et préventive jouent un rôle essentiel. Contrairement à la maintenance réactive, qui intervient après une panne, ces approches permettent d’anticiper les problèmes avant qu’ils ne surviennent. En surveillant continuellement les données collectées par les capteurs et en effectuant des contrôles réguliers, les entreprises peuvent éviter des interruptions coûteuses et maintenir un haut niveau de productivité.
Utilisation de l’intelligence artificielle et de l’IoT
L’intégration de l’Internet des objets (IoT) et de l’intelligence artificielle (IA) dans les systèmes automatisés révolutionne la manière dont les entreprises gèrent leur maintenance. Ces technologies permettent de collecter et d’analyser des données en temps réel, offrant une visibilité complète sur l’état des machines. Par exemple, les capteurs IoT installés sur un transtockeur ou un miniload peuvent surveiller des paramètres tels que la température, les vibrations et la vitesse. Si des anomalies sont détectées, le système peut générer des alertes en temps réel, permettant aux équipes de maintenance d’intervenir avant qu’un problème ne se transforme en panne.
L’IA permet d’analyser ces données massives et d’identifier des modèles qui échappent à l’œil humain. Grâce à des algorithmes avancés, l’IA peut prédire les pannes en fonction des signes avant-coureurs détectés dans les performances des machines. Cela permet non seulement d’optimiser la maintenance prédictive, mais aussi de planifier les interventions au moment le plus opportun, sans interrompre la production.
Plan de maintenance préventive efficace
Une maintenance préventive bien conçue repose sur un calendrier régulier d’inspections et d’interventions visant à éviter les pannes avant qu’elles ne surviennent. Cela inclut le remplacement des pièces usées, la lubrification des composants mécaniques et la mise à jour des logiciels. L’objectif est d’empêcher les dégradations qui, à long terme, pourraient entraîner des arrêts de production prolongés.
Un plan de maintenance efficace doit inclure des contrôles fréquents des systèmes de stockage automatisé. Les courroies, roulements et autres pièces mobiles doivent être régulièrement vérifiés et remplacés si nécessaire. Les logiciels doivent également être surveillés pour détecter toute anomalie ou erreur potentielle, et mis à jour pour intégrer les dernières améliorations en termes de sécurité et de performance.
En combinant une maintenance prédictive basée sur l’IA et une maintenance préventive bien planifiée, les entreprises peuvent prolonger la durée de vie de leurs systèmes automatisés et éviter des coûts imprévus liés aux pannes. Cette approche garantit un fonctionnement fluide et stable des opérations logistiques, permettant aux entreprises de rester compétitives et efficaces.
Les systèmes automatisés, bien qu’efficaces et robustes, ne sont pas à l’abri des dysfonctionnements. Repérer les signes avant-coureurs de problèmes est essentiel pour éviter des interruptions de production coûteuses et préserver la performance de ces systèmes. Qu’il s’agisse de baisse de performance, de dysfonctionnements mécaniques ou d’erreurs logicielles, chaque indicateur doit être surveillé de près. Grâce à l’intégration des technologies comme l’IoT et l’intelligence artificielle, les entreprises peuvent adopter des stratégies de maintenance prédictive et préventive, leur permettant d’anticiper les pannes et d’intervenir avant que les problèmes ne surviennent. En mettant en place un plan de maintenance rigoureux, associant la surveillance des capteurs et des interventions régulières, les entreprises peuvent maximiser la durée de vie et l’efficacité de leurs systèmes automatisés. Cela assure non seulement une meilleure rentabilité, mais aussi un gain de compétitivité à long terme dans un secteur de plus en plus axé sur l’automatisation.
Article généré par la technologie Open AI