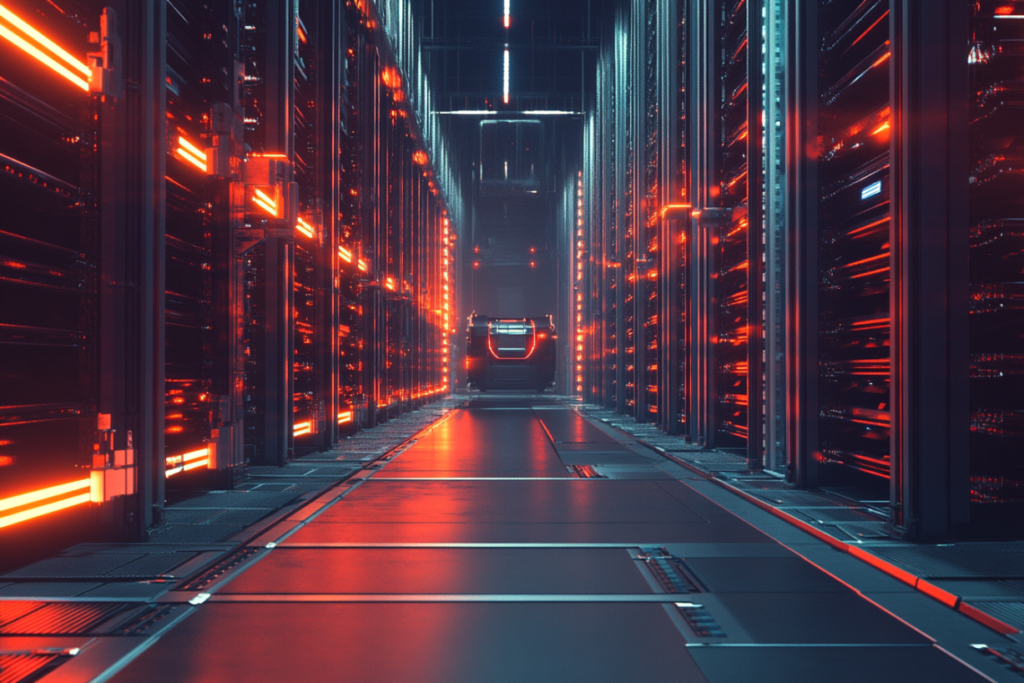
Dans le monde de la logistique moderne, où rapidité, précision et optimisation de l’espace sont des priorités, les systèmes de stockage automatisés jouent un rôle clé. Parmi ces solutions, le Miniload s’impose comme une technologie incontournable pour les entrepôts de toutes tailles. Grâce à sa capacité à gérer efficacement le stockage et la récupération des marchandises, ce système permet de maximiser la productivité tout en réduisant les coûts et les erreurs. Mais qu’est-ce qu’un Miniload exactement ? Comment fonctionne-t-il ? Quels sont ses avantages, ses inconvénients, et dans quels secteurs peut-il être le plus utile ? Cet article propose une exploration complète des systèmes Miniload, en abordant leurs caractéristiques techniques, leurs applications pratiques et les tendances qui façonnent leur évolution.
Définition : c’est quoi un Miniload ?
Le Miniload est un système de stockage automatisé conçu pour manipuler des unités de petite à moyenne taille, telles que des bacs, cartons ou caisses. Ce dispositif est particulièrement utilisé dans les entrepôts où l’optimisation de l’espace et la rapidité des opérations sont essentielles. Il se distingue par sa capacité à gérer efficacement un grand volume de marchandises, tout en assurant un accès rapide et précis à chaque article stocké.
Son fonctionnement repose sur un transstockeur automatisé, un robot qui se déplace horizontalement et verticalement dans des allées étroites. Ce robot assure le déplacement des unités entre leurs emplacements de stockage et les points de sortie ou d’entrée, le tout sous le contrôle d’un logiciel dédié.
Composants principaux du système de Miniload
Un système Miniload se compose de plusieurs éléments clés qui travaillent en synergie pour garantir son efficacité :
- Transstockeur automatisé : Cet équipement mobile, souvent équipé de bras télescopiques, permet de saisir ou déposer les unités de stockage.
- Rails et structures de stockage : Ces éléments définissent l’architecture du système, avec des rangées de rayonnages où les unités sont entreposées.
- Unité de contrôle informatique : Un logiciel central gère et optimise les mouvements du transstockeur en fonction des besoins de l’entrepôt.
- Supports de stockage : Ce sont les bacs, cartons ou caisses standardisés pour être compatibles avec le système.
- Interfaces utilisateur : Ces panneaux ou écrans permettent aux opérateurs de surveiller ou d’interagir avec le système en temps réel.
Le Miniload représente donc une avancée majeure dans le domaine de la logistique et du stockage, en associant technologie et ergonomie pour répondre aux besoins complexes des entrepôts modernes.
Fonctionnement d’un système Miniload
Le Miniload est conçu pour automatiser et simplifier les processus de stockage et de récupération dans les entrepôts. Chaque étape de son fonctionnement est pensée pour maximiser l’efficacité et réduire les temps d’attente. Plongeons dans les détails de ses mécanismes.
Processus de stockage et de récupération des Miniloads
Pour comprendre l’efficacité d’un Miniload, il est essentiel de détailler son processus central : la gestion des marchandises, de leur entrée dans le système à leur sortie.
- Entrée des marchandises : Lorsqu’un produit arrive dans l’entrepôt, il est placé dans un conteneur standardisé (bac, carton, caisse) et enregistré dans le système de gestion.
- Stockage automatisé : Le transstockeur se déplace vers l’emplacement désigné dans les rayonnages et y dépose le conteneur. L’emplacement est optimisé selon les règles du système (fréquence d’accès, poids, dimensions).
- Récupération des marchandises : Lorsqu’un produit est requis, le transstockeur localise son conteneur et le transporte jusqu’au point de sortie, où il est pris en charge par un opérateur ou un convoyeur automatique.
Rôle des transstockeurs automatisés
Au cœur de ce système, les transstockeurs jouent un rôle clé. Ces machines sophistiquées assurent le mouvement rapide et précis des conteneurs entre les rayonnages et les points de traitement. Leur importance réside dans leur capacité à fonctionner de manière fluide et continue, même dans les environnements les plus exigus.
Intégration avec le système de gestion d’entrepôt (WMS)
Pour garantir une performance optimale, le Miniload est intégré à un système de gestion d’entrepôt (WMS). Cette connexion permet une synchronisation complète entre les tâches du Miniload et les besoins opérationnels de l’entrepôt. Le WMS supervise l’ensemble des opérations, des priorités de traitement aux optimisations logistiques, pour garantir une gestion harmonieuse des flux de marchandises.
Caractéristiques techniques des miniloads
Les caractéristiques techniques d’un système Miniload en font une solution de stockage polyvalente et performante, adaptée aux exigences des entrepôts modernes. Explorons en détail les points clés qui définissent sa conception et son fonctionnement.
Capacité de charge d’un miniload
La capacité de charge d’un système Miniload dépend de sa conception, mais elle est généralement comprise entre 30 et 300 kg par unité de stockage. Ce seuil de poids le rend particulièrement adapté pour des marchandises légères à moyennes, telles que des pièces détachées, des composants électroniques, ou des produits emballés.
- Exemple concret : Dans l’industrie automobile, un Miniload peut gérer efficacement des pièces comme des vis, des filtres ou des capteurs. Ces articles, bien que légers, nécessitent une gestion rapide pour les opérations de montage.
En revanche, pour des produits plus volumineux ou lourds, comme des palettes entières ou des machines, des systèmes automatisés de type palettes sont préférables.
Dimensions et tailles typiques d’un miniload
Les Miniloads sont conçus pour s’intégrer dans des environnements où l’espace est précieux. Les dimensions typiques des structures varient en fonction des besoins, mais elles atteignent souvent entre 12 et 20 mètres de hauteur. Cela permet une exploitation verticale maximale, idéale pour des entrepôts urbains ou limités en superficie.
- Structure standardisée : Les rayonnages sont étroits, permettant des allées de seulement 1 à 2 mètres de large, ce qui améliore encore l’utilisation de l’espace.
- Modularité : Certains systèmes offrent une flexibilité d’ajout ou de réduction de niveaux de stockage en fonction de la croissance des besoins.
En résumé, les Miniloads s’adaptent parfaitement aux espaces restreints tout en maintenant une capacité de stockage impressionnante.
Vitesse de fonctionnement d’un miniload
L’un des atouts majeurs des Miniloads est leur rapidité. Les transstockeurs, éléments centraux du système, peuvent atteindre une vitesse de déplacement horizontal de 3 à 4 mètres par seconde, tandis que leur mouvement vertical oscille entre 1 et 2 mètres par seconde.
- Impact sur la productivité : Cette vitesse permet de traiter des centaines de cycles de stockage et de récupération par heure, réduisant considérablement les délais dans les entrepôts à forte rotation.
- Précision et fluidité : Grâce à des capteurs embarqués, les transstockeurs assurent des mouvements précis, limitant les risques de collisions ou d’erreurs dans le traitement des marchandises.
- Exemple concret : Un centre logistique e-commerce peut utiliser un Miniload pour gérer des flux continus, garantissant des délais de préparation de commandes très courts, même en période de forte activité comme le Black Friday.
Types de conteneurs utilisés pour le miniload
Un système Miniload est compatible avec une grande variété de conteneurs, à condition qu’ils respectent des standards définis pour garantir leur adaptabilité aux mécanismes. Ces supports incluent :
- Bacs en plastique rigide : Utilisés pour des produits fragiles ou nécessitant une protection accrue.
- Cartons renforcés : Idéaux pour des marchandises légères, comme les textiles ou les fournitures de bureau.
- Caisses métalliques : Recommandées pour des articles industriels ou des pièces de valeur nécessitant une sécurité accrue.
Chaque conteneur peut être équipé de codes-barres ou de puces RFID, permettant une identification rapide et un suivi précis des marchandises. Cela optimise également les inventaires en temps réel, intégrés au WMS.
Performances environnementales d’un miniload
Un aspect souvent négligé mais essentiel est la performance énergétique des Miniloads. Ces systèmes sont conçus pour minimiser leur consommation d’énergie grâce à des technologies de récupération d’énergie au freinage ou lors des descentes verticales.
- Exemple : Une entreprise ayant installé un Miniload équipé de moteurs à faible consommation a observé une réduction de 20 % de ses coûts énergétiques par rapport à des systèmes manuels ou semi-automatisés.
En conclusion, les caractéristiques techniques d’un Miniload le positionnent comme un choix stratégique pour les entreprises cherchant à optimiser leur espace, augmenter leur productivité et réduire leurs coûts énergétiques.
Avantages du Miniload
L’adoption d’un système Miniload offre une multitude d’avantages qui en font une solution privilégiée pour les entrepôts modernes. Ces bénéfices s’étendent de l’optimisation de l’espace à la sécurité des opérateurs, en passant par des gains significatifs en productivité. Explorons ces points en détail.
Optimisation de l’espace de stockage d’un entrepôt
L’un des principaux atouts du Miniload est sa capacité à maximiser l’utilisation de l’espace disponible dans un entrepôt.
- Structure verticale : En exploitant la hauteur du bâtiment, un Miniload permet de stocker plusieurs niveaux de bacs ou cartons, là où des systèmes manuels nécessiteraient des allées plus larges.
- Allées étroites : Les transstockeurs automatisés naviguent dans des allées très resserrées, réduisant l’espace inutilisé.
- Exemple concret : Une entreprise de distribution pharmaceutique a pu augmenter sa capacité de stockage de 40 % en installant un système Miniload dans son entrepôt existant, sans avoir à agrandir ses installations.
Augmentation de l’efficacité opérationnelle
Le Miniload simplifie et accélère considérablement les processus d’entrepôt grâce à son automatisation complète.
- Réduction des temps de traitement : Les transstockeurs, fonctionnant en continu, permettent de gérer des centaines de cycles de stockage et de récupération par heure.
- Amélioration du flux logistique : Les marchandises sont localisées et déplacées sans erreur, éliminant les temps d’attente inutiles pour les opérateurs.
- Exemple concret : Dans le secteur du e-commerce, l’intégration d’un Miniload a permis à un entrepôt de gérer 30 % de commandes supplémentaires pendant les périodes de pointe.
Amélioration de la précision des inventaires
La gestion informatisée des Miniloads garantit une précision optimale dans le suivi des stocks.
- Inventaire en temps réel : Chaque mouvement de conteneur est enregistré par le système de gestion, éliminant les risques d’erreurs humaines.
- Réduction des écarts d’inventaire : La localisation exacte des marchandises permet de minimiser les pertes ou les articles mal placés.
- Exemple concret : Une entreprise de pièces détachées a réduit ses erreurs d’inventaire de 95 % grâce à l’installation d’un système Miniload connecté à son logiciel WMS.
Réduction des erreurs de picking
Le picking, souvent sujet à des erreurs humaines, est drastiquement amélioré avec un Miniload.
- Guidage automatisé : Les transstockeurs apportent les marchandises directement aux points de picking, supprimant le besoin pour les opérateurs de parcourir l’entrepôt.
- Réduction des erreurs : Les opérateurs n’ont plus à localiser manuellement les articles, ce qui limite les risques de prélèvements incorrects.
- Exemple concret : Une entreprise spécialisée dans les équipements électroniques a constaté une diminution de 80 % des erreurs de picking après l’intégration d’un Miniload.
Sécurité accrue pour les opérateurs
Le Miniload minimise les risques d’accidents en réduisant les interventions manuelles dans les zones de stockage.
- Élimination des tâches dangereuses : Les transstockeurs remplacent les opérateurs pour accéder aux rayonnages en hauteur ou dans des espaces étroits.
- Réduction des troubles musculosquelettiques (TMS) : Les opérateurs n’ont plus à soulever de charges lourdes ou à adopter des postures inconfortables.
- Exemple concret : Une entreprise agroalimentaire a enregistré une baisse significative des accidents liés aux chutes et aux efforts physiques après l’automatisation de ses entrepôts avec un Miniload.
Économies à long terme pour l’entreprise
Bien que l’installation d’un Miniload représente un investissement initial conséquent, les économies réalisées à long terme compensent largement ce coût.
- Réduction des coûts de main-d’œuvre : Le besoin en personnel pour les opérations de stockage et de récupération diminue.
- Entretien optimisé : Les systèmes modernes nécessitent peu de maintenance et sont conçus pour une utilisation intensive sur plusieurs années.
- Exemple concret : Une entreprise de logistique a observé un retour sur investissement en moins de trois ans grâce aux économies réalisées sur les salaires et les gains de productivité.
En conclusion, les avantages du Miniload en font une solution de choix pour les entreprises cherchant à moderniser leurs opérations logistiques. Il combine performance, fiabilité et sécurité, tout en apportant des gains économiques et organisationnels.
Inconvénients du Miniload
Malgré ses nombreux avantages, le Miniload présente certains inconvénients qu’il est important de prendre en compte avant d’investir. Ces limitations peuvent influencer la décision d’adopter cette technologie selon les besoins et les contraintes de chaque entreprise.
Coût initial d’investissement élevé
L’un des principaux obstacles à l’implémentation d’un système Miniload réside dans son coût d’acquisition et d’installation. Ce type de technologie implique des dépenses importantes, incluant la conception sur mesure, l’achat des transstockeurs et la mise en œuvre des logiciels associés.
Les entreprises doivent souvent prévoir un budget conséquent pour couvrir :
- L’achat de l’équipement.
- Les travaux d’installation, parfois complexes.
- L’intégration avec les systèmes existants comme le WMS.
Cependant, ces coûts peuvent être justifiés par les économies réalisées à long terme, notamment en termes de productivité et de main-d’œuvre.
Limitations pour les produits de grande taille
Le Miniload est spécifiquement conçu pour gérer des articles de petite à moyenne taille. Par conséquent, il ne convient pas aux entreprises ayant un besoin de stockage pour des marchandises volumineuses ou des charges très lourdes.
Par exemple, les palettes industrielles ou les équipements surdimensionnés nécessitent d’autres types de systèmes, comme les transstockeurs pour palettes, qui offrent une capacité de charge plus importante.
Dépendance à la technologie et risques de pannes
L’automatisation accrue des Miniloads peut devenir une faiblesse en cas de panne ou de dysfonctionnement. Une interruption de service peut entraîner des retards significatifs dans les opérations logistiques, surtout si le système est mal entretenu ou s’il n’existe pas de plan de secours.
Les pannes fréquentes peuvent également engendrer des coûts imprévus liés :
- À l’intervention de techniciens spécialisés.
- Aux pièces de rechange spécifiques.
Il est donc essentiel de mettre en place un programme de maintenance rigoureux pour éviter ces désagréments.
Besoin de formation spécifique pour le personnel
L’introduction d’un système Miniload nécessite une formation approfondie pour les opérateurs et les responsables d’entrepôt. Ces derniers doivent se familiariser avec :
- Le fonctionnement des transstockeurs.
- Les interfaces du logiciel de gestion.
- Les procédures de maintenance basique.
Cette phase d’apprentissage peut ralentir temporairement les opérations, notamment dans les entreprises où le personnel est peu habitué aux technologies avancées.
Ces inconvénients ne remettent pas en question l’efficacité globale du Miniload, mais soulignent l’importance d’une préparation adéquate et d’une analyse approfondie avant son implémentation.
Applications et secteurs d’utilisation des Miniloads
Le Miniload est une solution polyvalente qui trouve sa place dans de nombreux secteurs industriels et commerciaux. Son efficacité, sa précision et son adaptabilité en font un choix populaire pour optimiser la gestion des entrepôts. Examinons les domaines où cette technologie est particulièrement performante et ses usages concrets.
Industries les plus adaptées au Miniload
Le Miniload est conçu pour répondre aux besoins spécifiques de certaines industries où la manipulation de marchandises légères et moyennes est primordiale. Parmi les secteurs les plus adaptés, on trouve :
- E-commerce : Avec un fort besoin de rapidité dans la préparation des commandes, le Miniload garantit des délais réduits et une précision accrue dans le secteur du e-commerce.
- Industrie pharmaceutique : Idéal pour stocker et récupérer des produits sensibles tels que des médicaments ou des équipements médicaux.
- Automobile : Utilisé pour la gestion des pièces détachées et des composants, il facilite le réapprovisionnement des lignes de production.
- Distribution alimentaire : Parfait pour manipuler des denrées emballées ou conditionnées, notamment dans les entrepôts à température contrôlée.
- Électronique : Adapté pour le stockage de composants de haute valeur nécessitant une manipulation soignée.
Ces industries bénéficient de l’optimisation de l’espace et de la vitesse opérationnelle qu’offre le Miniload.
Exemples concrets d’utilisation d’un miniload dans différents secteurs
- E-commerce : Un géant du commerce en ligne a déployé des Miniloads pour automatiser le traitement des commandes pendant le Black Friday. Résultat : une augmentation de 40 % des commandes expédiées en temps record.
- Automobile : Dans une usine de production, un système Miniload a permis de réduire les interruptions de la chaîne d’assemblage en assurant une livraison rapide des pièces nécessaires.
- Pharmaceutique : Une entreprise spécialisée dans les vaccins utilise des Miniloads dans ses entrepôts frigorifiques pour maintenir l’intégrité des produits tout en optimisant les cycles de récupération.
Polyvalence du miniload dans les environnements complexes
Le Miniload s’adapte également aux environnements spécifiques grâce à des options personnalisées. Par exemple :
- Entrepôts à température contrôlée : Les transstockeurs peuvent fonctionner dans des environnements réfrigérés pour gérer des marchandises sensibles.
- Sites à espace restreint : Grâce à sa structure verticale, le Miniload est particulièrement utile dans les entrepôts urbains où chaque mètre carré compte.
En conclusion, le Miniload est une solution qui s’intègre parfaitement dans divers secteurs d’activité, apportant des bénéfices tangibles en termes de performance et d’efficacité.
Comparaison du miniload avec d’autres systèmes de stockage automatisé
Pour bien évaluer l’intérêt d’un Miniload, il est essentiel de le comparer à d’autres systèmes de stockage, qu’ils soient manuels ou automatisés. Cette analyse permet de mieux comprendre ses avantages et ses limites face à d’autres technologies.
Miniload vs systèmes de stockage manuels
Les systèmes de stockage manuels, bien que couramment utilisés, montrent rapidement leurs limites dans les environnements à forte activité. Voici une comparaison des deux approches :
- Efficacité opérationnelle :
Un système manuel dépend fortement de la rapidité et de la précision des opérateurs. En revanche, le Miniload élimine les interventions humaines pour le stockage et la récupération, réduisant ainsi les temps de traitement et les erreurs. - Utilisation de l’espace :
Les Miniloads exploitent la verticalité des entrepôts, là où les systèmes manuels nécessitent des allées larges pour les chariots élévateurs, entraînant une perte d’espace. - Coût :
Les systèmes manuels sont initialement moins coûteux, mais à long terme, les économies réalisées grâce à l’automatisation du Miniload (réduction des erreurs, main-d’œuvre, et temps) compensent largement l’investissement initial.
Miniload vs autres systèmes automatisés (ex : Shuttle ou Pallet Load)
Les Miniloads sont souvent comparés à d’autres systèmes automatisés comme les Shuttles ou les Pallet Loads. Ces technologies répondent à des besoins différents et s’adressent à des types de marchandises spécifiques.
- Types de marchandises :
Le Miniload est idéal pour les articles de petite à moyenne taille, tandis que les Pallet Loads sont conçus pour des charges volumineuses ou lourdes, comme des palettes industrielles. Les Shuttles, quant à eux, excellent dans le traitement des marchandises à haute rotation. - Vitesse :
Les Shuttles sont généralement plus rapides que les Miniloads pour des distances courtes, mais le Miniload conserve un avantage en termes de précision et de gestion d’un large éventail de produits. - Flexibilité :
Le Miniload est souvent préféré pour les environnements nécessitant une gestion flexible des stocks, tandis que les Pallet Loads conviennent mieux aux installations spécialisées dans des articles homogènes.
Positionnement stratégique du miniload
En résumé, le choix d’un système dépend des besoins spécifiques de l’entreprise :
- Pour un entrepôt traitant de nombreux petits articles et nécessitant un haut degré de précision, le Miniload est idéal.
- Pour des charges lourdes ou volumineuses, un Pallet Load sera plus adapté.
- Si la priorité est la vitesse pour des articles à forte rotation, les Shuttles seront plus efficaces.
Cette comparaison met en lumière la polyvalence du Miniload, qui combine performance, précision et adaptabilité dans un large éventail de scénarios logistiques.
Critères de choix d’un système Miniload
Avant d’investir dans un système Miniload, il est crucial d’évaluer plusieurs critères pour s’assurer qu’il correspond parfaitement aux besoins spécifiques de votre entreprise. Une analyse approfondie garantit une implémentation réussie et un retour sur investissement optimal.
Facteurs à considérer avant l’implémentation d’un miniload
- Nature des marchandises stockées :
Les Miniloads sont conçus pour manipuler des bacs ou des cartons de taille et de poids standards. Si vos marchandises comprennent des articles volumineux ou lourds, d’autres systèmes automatisés pourraient être plus adaptés. - Taille de l’entrepôt :
Les entrepôts ayant une hauteur disponible importante bénéficient particulièrement du Miniload grâce à sa structure verticale, qui maximise l’utilisation de l’espace. - Volumétrie des flux :
Si votre activité implique un grand nombre de cycles de stockage et de récupération quotidien, le Miniload est idéal pour garantir rapidité et fluidité des opérations. Pour des besoins moins intensifs, une solution semi-automatisée pourrait suffire. - Budget :
Bien que l’investissement initial soit conséquent, il est important de calculer le coût total de possession (TCO) en tenant compte des économies réalisées sur la main-d’œuvre et les erreurs à long terme. - Intégration avec les systèmes existants :
Assurez-vous que le Miniload peut être intégré facilement avec votre système de gestion d’entrepôt (WMS) et vos autres équipements automatisés.
Évaluation des besoins spécifiques de l’entreprise
Pour garantir une implémentation réussie, il est essentiel d’analyser en détail les besoins spécifiques de votre activité. Définir des objectifs opérationnels clairs, comme réduire les délais de préparation de commande ou améliorer la précision des inventaires, permettra de sélectionner le Miniload le mieux adapté.
Si vous prévoyez une croissance future de vos volumes, optez pour un système évolutif qui peut s’adapter à vos besoins sans nécessiter un remplacement complet. Par exemple, une entreprise de e-commerce ayant intégré un Miniload évolutif a pu augmenter sa capacité de traitement de 50 % en seulement deux ans sans investir dans une nouvelle infrastructure.
La compatibilité avec les contraintes spécifiques de l’industrie est également un critère clé. Les entreprises du secteur pharmaceutique, par exemple, doivent tenir compte des réglementations strictes liées à la traçabilité des produits.
Processus d’installation et de mise en œuvre du Miniload
L’installation d’un système Miniload nécessite une planification rigoureuse et un suivi précis pour garantir une intégration réussie dans l’environnement d’entrepôt existant. Chaque étape du processus contribue à maximiser la performance du système et à réduire les risques d’interruption des opérations.
Étapes de l’implémentation d’un miniload
Le processus débute par une analyse approfondie des besoins. Cette phase consiste à évaluer les flux logistiques, les volumes de stockage nécessaires et les caractéristiques des marchandises à manipuler. Cette analyse permet de concevoir une solution adaptée aux spécificités de l’entreprise. Une fois cette étape validée, le projet entre dans sa phase de planification.
La planification inclut la création d’un plan détaillé d’implantation. Ce document identifie les emplacements exacts des rayonnages, les zones de manutention et les points de connexion aux autres équipements de l’entrepôt, comme les convoyeurs ou les systèmes de gestion d’entrepôt (WMS). Une coordination étroite entre le fournisseur du système et l’entreprise est essentielle à ce stade.
L’installation physique constitue la troisième étape. Les rayonnages, rails et transstockeurs sont assemblés sur site par une équipe spécialisée. Cette phase peut s’étendre sur plusieurs semaines en fonction de la taille du projet. Parallèlement, les systèmes logiciels sont configurés et testés pour garantir leur compatibilité avec les processus de l’entrepôt.
Enfin, la mise en service intervient. Cette étape inclut des tests à vide et en conditions réelles pour vérifier que le système répond aux exigences de performance et de fiabilité définies lors de la planification. Les ajustements nécessaires sont apportés avant que le système ne devienne pleinement opérationnel.
Temps moyen d’installation et de configuration d’un miniload
Le temps nécessaire pour installer un Miniload dépend de la complexité du projet et de la taille de l’installation. En général, une petite installation peut être opérationnelle en 4 à 6 semaines, tandis que des projets plus complexes, incluant une forte intégration logicielle, peuvent nécessiter 2 à 3 mois.
Un exemple typique serait un entrepôt de taille moyenne qui installe un Miniload pour gérer ses flux de pièces détachées. Le système, comprenant deux transstockeurs et 1 000 emplacements de stockage, a été configuré et testé en seulement huit semaines, réduisant ainsi les interruptions des opérations existantes.
Importance du support technique pendant l’installation du miniload
Un support technique constant est indispensable pour résoudre rapidement les éventuels problèmes qui peuvent survenir durant l’installation. Les fournisseurs expérimentés proposent souvent des équipes dédiées pour superviser la mise en œuvre et former le personnel à l’utilisation et à la maintenance du système.
Avec une planification adéquate et une collaboration étroite entre les parties impliquées, le processus d’installation d’un Miniload peut se dérouler efficacement, garantissant une transition en douceur vers un entrepôt automatisé.
Maintenance et entretien des miniloads
La maintenance d’un système Miniload est essentielle pour garantir sa performance et sa durabilité. Bien qu’il s’agisse d’un système automatisé, il nécessite des interventions régulières pour prévenir les pannes, assurer la sécurité et maintenir un fonctionnement optimal.
Exigences de maintenance régulière d’un miniload
La maintenance préventive est un élément clé pour limiter les interruptions et éviter les coûts élevés associés aux réparations d’urgence. Les principales tâches incluent :
- Inspection des transstockeurs : Vérification des moteurs, des câbles, et des capteurs pour s’assurer qu’ils fonctionnent correctement.
- Contrôle des rails et des structures : S’assurer que les rails sont alignés et exempts de tout obstacle pouvant gêner le déplacement des transstockeurs.
- Mise à jour des logiciels : Installer régulièrement les mises à jour pour optimiser les performances du système et renforcer la sécurité informatique.
- Lubrification des pièces mobiles : Réduire l’usure et prolonger la durée de vie des composants mécaniques.
Une maintenance préventive bien planifiée peut réduire les coûts de réparation jusqu’à 30 % et augmenter la durée de vie globale du système.
Gestion des pannes et support technique d’un miniload
Malgré une maintenance régulière, des pannes peuvent survenir en raison de l’usure naturelle ou de problèmes imprévus. Dans ce cas, une gestion rapide est essentielle pour minimiser les impacts sur les opérations. Les solutions incluent :
- Diagnostic rapide : Grâce aux capteurs intégrés, les Miniloads peuvent identifier les anomalies et transmettre des alertes au système de gestion.
- Intervention d’experts : Les fournisseurs de systèmes Miniload proposent souvent des contrats de maintenance avec des techniciens spécialisés capables d’intervenir rapidement sur site.
- Pièces de rechange disponibles : Un stock local de pièces critiques, comme les courroies ou les capteurs, peut accélérer les réparations et réduire les temps d’arrêt.
Un exemple concret serait une entreprise de logistique ayant subi une panne de transstockeur lors de sa période de pointe. Grâce à un contrat de maintenance premium, un technicien est intervenu dans les deux heures, limitant ainsi les interruptions à une demi-journée.
Fréquence et planification des interventions sur le miniload
La fréquence des interventions dépend de l’intensité d’utilisation du système. En général, il est recommandé de procéder à une maintenance préventive tous les trois à six mois. Pour les systèmes très sollicités, comme ceux des entrepôts de distribution, des inspections mensuelles peuvent être nécessaires.
Planifier ces interventions en dehors des heures de pointe ou lors de périodes de faible activité permet de réduire les perturbations opérationnelles.
Bénéfices à long terme d’un miniload
Une maintenance rigoureuse assure non seulement la pérennité du système, mais contribue également à des gains indirects, tels qu’une productivité accrue, une sécurité améliorée et une meilleure satisfaction des clients grâce à une fiabilité opérationnelle constante.
Évolutions technologiques et tendances futures des miniloads
Le Miniload, déjà reconnu pour son efficacité, continue d’évoluer grâce à l’intégration de technologies de pointe. Ces innovations renforcent ses performances, élargissent ses applications et répondent aux besoins croissants des entrepôts modernes. Voici un aperçu des avancées récentes et des tendances qui façonnent son avenir.
Innovations récentes dans les systèmes Miniload
L’automatisation du Miniload s’améliore sans cesse grâce à l’adoption de technologies avancées. Parmi les innovations notables :
- Intelligence artificielle (IA) : L’intégration de l’IA dans les systèmes Miniload permet une analyse prédictive des flux de marchandises. En anticipant les pics d’activité et en optimisant les mouvements, l’IA réduit les temps d’attente et améliore l’utilisation de l’espace.
- Capteurs intelligents : Les capteurs embarqués permettent un suivi en temps réel de l’état des transstockeurs et des marchandises. Cela contribue à améliorer la précision et à détecter les anomalies avant qu’elles n’entraînent des pannes.
- Efficacité énergétique : De nouveaux moteurs et systèmes de récupération d’énergie réduisent la consommation électrique du Miniload, le rendant plus respectueux de l’environnement.
Ces avancées technologiques rendent le Miniload encore plus fiable et performant, tout en réduisant son empreinte écologique.
Perspectives d’avenir et améliorations potentielles des miniloads
Les tendances futures des systèmes Miniload visent à répondre aux exigences croissantes des entreprises en matière de flexibilité, de rapidité et de durabilité. Voici les axes de développement les plus prometteurs :
- Modularité accrue : Les Miniloads pourraient être conçus avec des modules interchangeables, permettant aux entreprises d’ajuster leur capacité de stockage et leur configuration en fonction de l’évolution de leurs besoins.
- Automatisation totale : La combinaison des Miniloads avec des robots collaboratifs (cobots) pour les opérations de picking pourrait éliminer complètement les interventions humaines dans certains entrepôts.
- Intégration avec la chaîne logistique connectée : Les systèmes Miniloads pourraient être reliés à des plateformes logistiques globales, offrant une visibilité en temps réel sur l’ensemble des flux de marchandises.
Exemples concrets d’améliorations à venir
Dans certains entrepôts pilotes, des Miniloads dotés de caméras 3D analysent en temps réel la qualité des marchandises stockées, détectant les éventuels défauts ou endommagements. Ces systèmes pourraient devenir la norme, offrant une nouvelle dimension de contrôle qualité.
Les avancées en intelligence artificielle permettent également de prioriser les tâches en fonction des urgences et des délais de livraison, un atout majeur pour les secteurs comme le e-commerce.
Impact de ces évolutions sur les entreprises
Ces améliorations technologiques renforcent non seulement la compétitivité des entreprises, mais leur permettent également de répondre plus efficacement aux attentes de leurs clients. Un Miniload de nouvelle génération offre des performances supérieures et une rentabilité accrue, tout en s’inscrivant dans une démarche durable et innovante.
Aspects économiques desquels tenir compte à propos des Miniloads
L’investissement dans un système Miniload représente un engagement financier significatif, mais il s’agit également d’un choix stratégique qui peut générer des bénéfices considérables à long terme. Analyser les coûts et le retour sur investissement (ROI) est essentiel pour évaluer la rentabilité de ce type de système.
Analyse coût-bénéfice d’un miniload
L’installation d’un Miniload implique des coûts directs et indirects qui doivent être comparés aux avantages économiques qu’il procure.
Coûts d’installation :
- Acquisition de l’équipement : Les transstockeurs, rails, et logiciels de gestion représentent une part importante du budget initial.
- Travaux d’aménagement : Inclut la préparation de l’entrepôt et l’intégration des infrastructures.
- Formation du personnel : Des sessions de formation sont nécessaires pour familiariser les opérateurs avec le système.
Bénéfices économiques :
- Réduction des coûts de main-d’œuvre : L’automatisation limite le recours à un grand nombre d’opérateurs pour les tâches de stockage et de picking.
- Diminution des erreurs : Les erreurs de gestion de stocks et de prélèvement, souvent coûteuses, sont réduites grâce à la précision du système.
- Optimisation de l’espace : La capacité à stocker davantage de marchandises dans un espace réduit permet d’éviter des coûts liés à l’agrandissement des entrepôts.
Un exemple concret d’entreprise ayant adopté un Miniload a montré une réduction de 25 % de ses coûts de fonctionnement dès la première année d’utilisation.
Retour sur investissement (ROI) typique d’un miniload
Le ROI d’un système Miniload varie en fonction de la taille de l’installation et du secteur d’activité. En général, le retour sur investissement est atteint en 3 à 5 ans.
Facteurs influençant le ROI :
- Le volume d’activité de l’entrepôt.
- La complexité des flux logistiques.
- Les économies réalisées sur la main-d’œuvre et les erreurs.
Par exemple, une entreprise de distribution ayant investi dans un Miniload pour gérer des commandes à haute rotation a observé un ROI en 3 ans grâce à une augmentation de 40 % de sa productivité et à une diminution significative des erreurs de picking.
Avantages économiques à long terme d’un miniload
Au-delà du ROI initial, un système Miniload offre des bénéfices continus sur le long terme.
- Économies énergétiques : Les systèmes modernes consomment moins d’énergie grâce à des technologies de récupération.
- Réduction des coûts de maintenance : Bien que régulière, la maintenance des Miniloads est généralement moins coûteuse que celle des équipements manuels ou semi-automatisés.
- Amélioration de la satisfaction client : Une meilleure gestion des stocks et des délais plus courts se traduisent par une fidélité accrue des clients et une augmentation des ventes.
En résumé, bien qu’exigeant un investissement initial important, un système Miniload est une solution économiquement viable pour les entreprises souhaitant optimiser leurs entrepôts tout en augmentant leur productivité.
Impact environnemental des Miniloads
Les systèmes Miniloads, en plus de leurs avantages économiques et opérationnels, jouent un rôle de plus en plus important dans les efforts de durabilité et de réduction de l’empreinte écologique des entrepôts. Leur conception intègre des technologies et des pratiques qui contribuent à des opérations plus respectueuses de l’environnement.
Efficacité énergétique des systèmes Miniload
L’un des principaux atouts environnementaux des Miniloads réside dans leur faible consommation d’énergie, notamment grâce à des innovations spécifiques :
- Technologies de récupération d’énergie : Les transstockeurs récupèrent l’énergie générée lors des descentes ou des freinages, qui est réinjectée dans le système pour réduire la consommation globale.
- Moteurs à haute efficacité : Les moteurs modernes, utilisés pour les déplacements horizontaux et verticaux, consomment moins d’électricité tout en maintenant des performances élevées.
- Gestion intelligente de l’énergie : Les logiciels de contrôle optimisent les mouvements des transstockeurs pour éviter les trajets inutiles, ce qui réduit la consommation énergétique globale.
Un exemple concret est celui d’un entrepôt logistique qui, après avoir adopté un Miniload, a réduit ses coûts énergétiques de 20 %, contribuant ainsi à une diminution significative de son empreinte carbone.
Contribution à la réduction de l’empreinte carbone
Les Miniloads participent à une logistique plus écologique de plusieurs façons :
- Réduction des déplacements manuels : En automatisant les tâches de stockage et de récupération, les Miniloads diminuent l’utilisation de chariots élévateurs et autres équipements énergivores.
- Optimisation de l’espace : En permettant un stockage vertical intensif, ils réduisent le besoin d’agrandir les entrepôts ou d’utiliser des espaces supplémentaires, limitant ainsi l’impact environnemental des nouvelles constructions.
- Diminution des déchets : La précision des systèmes réduit les erreurs, et donc les pertes de marchandises et les déchets associés.
Dans le cadre de la logistique verte, certaines entreprises combinent les Miniloads avec d’autres technologies durables, comme les panneaux solaires pour alimenter les entrepôts, créant ainsi des installations quasi autonomes en énergie.
Perspectives environnementales à long terme
Les Miniloads s’inscrivent dans une démarche globale de réduction de l’impact environnemental des chaînes d’approvisionnement. À l’avenir, ils pourraient intégrer davantage de matériaux recyclés dans leur construction et exploiter des sources d’énergie renouvelable pour leur fonctionnement.
Les entreprises qui adoptent ces systèmes renforcent leur engagement environnemental, ce qui est non seulement bénéfique pour la planète, mais aussi un argument commercial fort auprès de clients sensibles à la durabilité.
Intégration avec d’autres technologies d’entrepôt
Les systèmes Miniloads s’intègrent parfaitement dans un environnement logistique moderne où l’automatisation et la connectivité jouent un rôle central. Leur compatibilité avec d’autres technologies d’entrepôt renforce leur efficacité et élargit leur champ d’application.
Compatibilité avec les systèmes de gestion d’entrepôt (WMS)
Le Miniload fonctionne en étroite collaboration avec le système de gestion d’entrepôt (WMS), un logiciel essentiel pour orchestrer les opérations logistiques. Cette intégration permet :
- Une synchronisation des flux : Le WMS transmet les informations sur les articles à stocker ou à récupérer, permettant au Miniload d’agir en temps réel.
- Une optimisation des emplacements : Le WMS peut analyser la fréquence d’accès des marchandises pour leur attribuer les emplacements les plus adaptés, améliorant ainsi l’efficacité globale.
- Un suivi précis des stocks : Grâce à l’interaction entre le WMS et le Miniload, chaque mouvement de marchandises est enregistré, assurant une gestion des stocks en temps réel.
Par exemple, dans un entrepôt de e-commerce, un WMS connecté à un Miniload a permis d’augmenter la précision des commandes à 99 %, réduisant les erreurs et améliorant la satisfaction client.
Interaction avec d’autres équipements automatisés
Le Miniload peut également être intégré à une variété d’équipements automatisés pour former un système logistique entièrement connecté. Parmi ces équipements :
- Convoyeurs automatiques : Ces dispositifs transportent les marchandises depuis les points de stockage du Miniload jusqu’aux zones de préparation des commandes ou d’expédition.
- Robots mobiles autonomes (AMR) : Les AMR collaborent avec le Miniload pour déplacer les bacs ou cartons dans l’entrepôt, offrant une flexibilité accrue dans les flux de marchandises.
- Systèmes de tri automatisés : Les articles récupérés par le Miniload peuvent être acheminés vers des trieurs pour un dispatching rapide vers différentes destinations.
Ces interactions créent une chaîne logistique fluide et optimisée, où chaque élément contribue à réduire les temps d’attente et à augmenter la productivité.
Exemples concrets d’intégration
Un centre logistique combinant Miniloads et robots AMR a pu réduire de 50 % les déplacements inutiles, augmentant ainsi l’efficacité et réduisant les coûts opérationnels. De plus, un entrepôt alimentaire équipé de convoyeurs automatiques et de Miniloads a réussi à doubler sa capacité de traitement des commandes pendant les périodes de forte demande.
Bénéfices globaux de l’intégration d’un miniload
L’intégration des Miniloads avec d’autres technologies permet une gestion centralisée et harmonieuse des opérations logistiques. Elle favorise également la scalabilité, rendant l’entrepôt capable de s’adapter aux besoins croissants des entreprises modernes.
Considérations de sécurité et réglementations autour des miniloads
La mise en place d’un système Miniload dans un entrepôt nécessite une attention particulière à la sécurité et au respect des réglementations en vigueur. Ces aspects sont essentiels pour garantir non seulement la protection des opérateurs, mais aussi la conformité légale de l’installation.
Normes de sécurité à respecter
Les Miniloads, comme tout système automatisé, doivent répondre à des normes de sécurité strictes. Ces normes visent à prévenir les accidents et à minimiser les risques associés à l’utilisation de machines en mouvement. Parmi les exigences principales :
- Présence de barrières de sécurité : Les zones où opèrent les transstockeurs doivent être clairement délimitées pour empêcher l’accès non autorisé.
- Capteurs et dispositifs d’arrêt d’urgence : Les transstockeurs doivent être équipés de capteurs détectant les obstacles et d’interrupteurs d’urgence permettant de stopper immédiatement le système en cas de danger.
- Formation des opérateurs : Les employés travaillant à proximité du Miniload doivent être formés aux consignes de sécurité et à l’utilisation correcte des équipements.
Par exemple, une entreprise logistique ayant installé un Miniload a mis en place des formations trimestrielles pour son personnel afin de réduire les risques d’accidents liés à une mauvaise manipulation.
Réglementations spécifiques selon les pays ou industries
Les réglementations varient selon les régions et les secteurs d’activité, mais elles couvrent généralement des aspects similaires. Voici quelques exemples :
- Union Européenne : La directive Machines 2006/42/CE impose des exigences sur la conception et l’utilisation des équipements automatisés, notamment en termes de sécurité des opérateurs.
- Secteur pharmaceutique : Des normes spécifiques, comme les Bonnes Pratiques de Fabrication (BPF), exigent un contrôle rigoureux des processus automatisés, y compris la traçabilité des marchandises stockées.
- Industries à risques spécifiques : Dans les secteurs manipulant des substances dangereuses ou inflammables, des règles supplémentaires sur la conception des Miniloads peuvent s’appliquer, telles que l’utilisation de matériaux ignifuges.
Le respect de ces réglementations est essentiel pour éviter les sanctions et garantir le bon fonctionnement des opérations.
Avantages d’une mise en conformité rigoureuse
En respectant les normes et réglementations, les entreprises bénéficient de plusieurs avantages :
- Réduction des risques d’accidents : Une installation conforme minimise les dangers pour les employés.
- Amélioration de la productivité : Les interruptions dues à des inspections ou à des incidents sont réduites.
- Renforcement de la réputation : Une entreprise respectant les standards de sécurité renforce sa crédibilité auprès de ses partenaires et clients.
En intégrant ces considérations dès la phase de conception du projet, les entreprises peuvent s’assurer que leur système Miniload est non seulement performant, mais aussi conforme aux exigences légales et sécuritaires.
Formation et ressources humaines au miniload
L’intégration d’un système Miniload dans un entrepôt nécessite une adaptation organisationnelle et un investissement en formation pour le personnel. Ces mesures garantissent une transition fluide et optimisent l’utilisation de cette technologie automatisée.
Compétences requises pour opérer un système Miniload
L’utilisation d’un système Miniload exige des compétences techniques et une bonne compréhension des processus automatisés. Les principales compétences nécessaires incluent :
- Maîtrise des logiciels : Les opérateurs doivent être capables d’interagir avec le système de gestion d’entrepôt (WMS) pour suivre les stocks, générer des rapports et résoudre les anomalies.
- Connaissances en maintenance de base : Il est essentiel que le personnel puisse identifier des problèmes mineurs, comme une erreur de calibration, et effectuer des vérifications simples pour éviter des pannes coûteuses.
- Sens de l’organisation : Une compréhension claire des flux logistiques et des priorités opérationnelles aide les opérateurs à maximiser l’efficacité du système.
Programmes de formation nécessaires
L’introduction d’un Miniload nécessite un programme de formation structuré pour le personnel concerné. Ce programme peut inclure :
- Formation initiale : Une introduction complète au fonctionnement du système, couvrant la gestion des transstockeurs, l’utilisation des logiciels et les consignes de sécurité.
- Sessions de perfectionnement : Des formations périodiques pour approfondir les connaissances et intégrer les mises à jour technologiques ou logicielles.
- Simulations pratiques : Des exercices en conditions réelles pour permettre au personnel de se familiariser avec le système avant son utilisation quotidienne.
Par exemple, une entreprise de distribution a réduit de 50 % les erreurs liées à la gestion du Miniload en organisant une formation mensuelle pour ses opérateurs sur les meilleures pratiques.
Impact sur l’organisation du travail dans l’entrepôt
La mise en place d’un Miniload modifie l’organisation des tâches dans un entrepôt. Les opérateurs passent moins de temps à effectuer des tâches physiques, comme le déplacement de marchandises, et davantage à superviser les processus automatisés.
- Réduction des efforts physiques : Les employés sont libérés des tâches répétitives et fatigantes, ce qui diminue les risques de troubles musculosquelettiques (TMS).
- Création de nouveaux rôles : Avec l’automatisation, de nouveaux postes émergent, comme celui de coordinateur de systèmes automatisés ou de technicien de maintenance.
- Amélioration de la productivité : En se concentrant sur des tâches à plus forte valeur ajoutée, les équipes peuvent contribuer directement à l’optimisation des flux logistiques.
Avantages pour les ressources humaines
Investir dans la formation et la montée en compétences des employés présente plusieurs avantages pour l’entreprise :
- Réduction du turnover : Offrir des opportunités de développement professionnel fidélise les employés et améliore leur satisfaction.
- Renforcement de l’efficacité : Un personnel bien formé est capable de maximiser les performances du système tout en réduisant les erreurs.
- Adaptation aux évolutions futures : Les employés formés peuvent rapidement s’adapter aux mises à jour technologiques ou aux nouvelles configurations de l’entrepôt.
Avec une formation adéquate et une gestion proactive des ressources humaines, l’introduction d’un système Miniload devient une opportunité d’évolution pour l’ensemble de l’équipe.
Le Miniload s’impose comme une solution incontournable pour les entrepôts modernes, alliant automatisation, optimisation de l’espace et efficacité opérationnelle. Avec sa capacité à gérer un large éventail de marchandises, il répond aux besoins variés des industries telles que l’e-commerce, la distribution pharmaceutique ou encore l’automobile. Cependant, son adoption nécessite une analyse approfondie des besoins, un investissement initial conséquent et une attention particulière à la formation du personnel. En retour, les entreprises bénéficient d’un système qui améliore la productivité, réduit les erreurs, renforce la sécurité et s’inscrit dans une démarche durable grâce à ses performances énergétiques. Les évolutions technologiques et l’intégration croissante avec d’autres équipements et logiciels renforcent encore son attractivité, en faisant un choix stratégique pour toute entreprise souhaitant moderniser sa logistique. En somme, le Miniload représente un atout majeur pour répondre aux défis des entrepôts de demain, tout en offrant un retour sur investissement tangible et une adaptabilité à long terme. Si vous cherchez à transformer votre chaîne logistique, le Miniload pourrait être la clé de votre succès.
Article généré par la technologie Open AI